Thin-walled aluminum tubes quietly thread their way through our lives, from the sleek frames of bicycles to the hidden guts of electronics. Their deceptively simple form belies a remarkable versatility and a significant impact on the world around us. But what exactly are these humble tubes, and why do they matter so much? Let’s delve into the fascinating world of thin-walled aluminum, exploring its unique properties, and diverse applications.
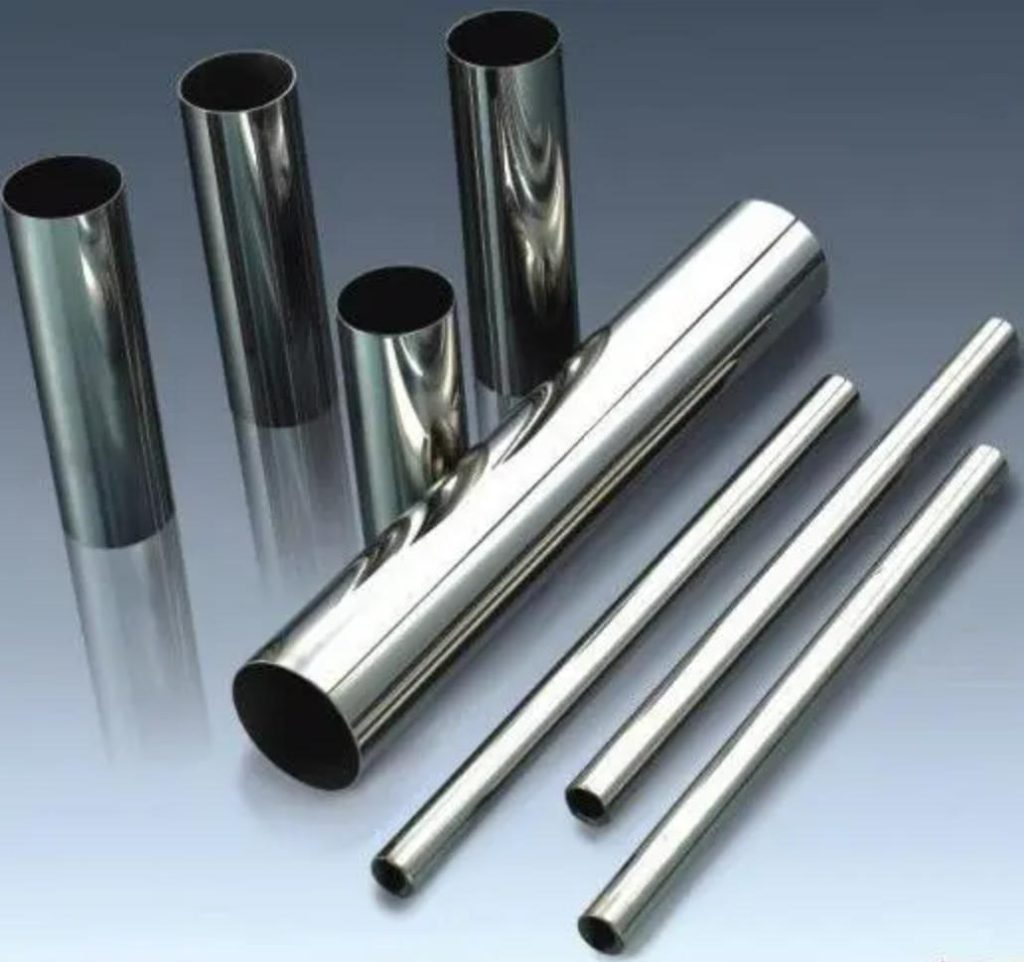
What are Thin-Walled Aluminum Tubes?
As the name suggests, thin-walled aluminum tubes are essentially aluminum tubes with a relatively thin wall compared to their diameter. This wall thickness can range from a fraction of a millimeter to a few millimeters, depending on the intended application.
Manufacturing Process of Thin-Walled Aluminum Tubes:
These tubes are typically manufactured through two main methods:
- Extrusion: Molten aluminum is forced through a die with the desired tube profile, creating a seamless tube with a consistent wall thickness.
- Drawing: Pre-existing aluminum tubes are drawn through progressively smaller dies, thinning the walls and achieving the desired diameter and wall thickness.
Types of Thin-Walled Aluminum Tubes:
Thin-walled aluminum tubes come in a variety of shapes and sizes, catering to diverse needs. Some common types include:
From Shapes:
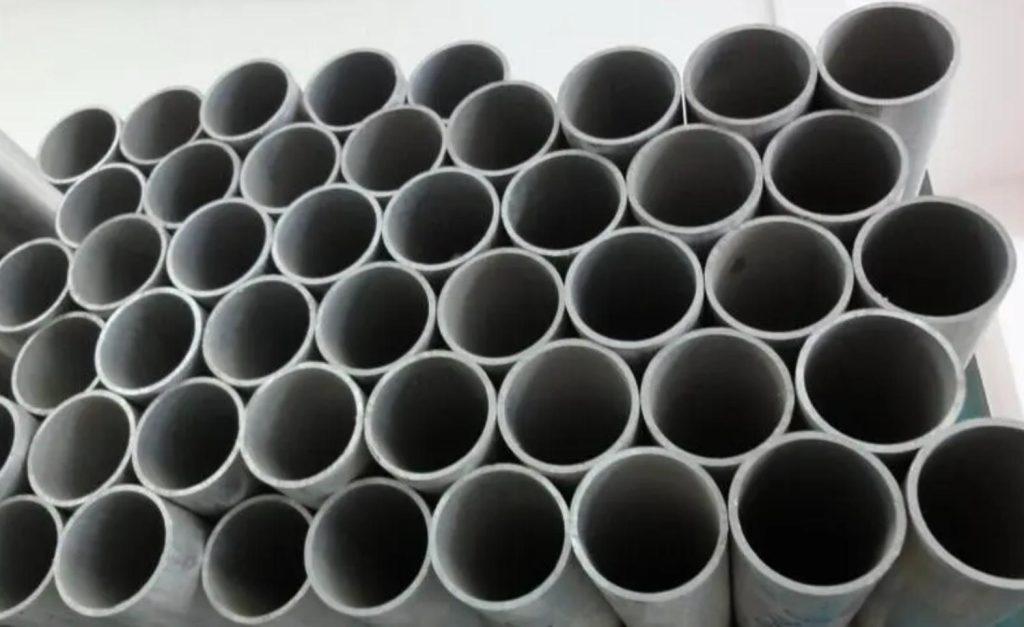
- Round: This is the most common shape, offering good structural integrity and ease of manufacturing.
- Square: Square tubes provide high torsional rigidity and are often used in structural applications.
- Rectangular: Similar to square tubes, but with different width and height dimensions, offering more design flexibility.
- Triangular: Triangular tubes offer unique aesthetic appeal and can be used for lightweight structural applications.
- Oval: Oval tubes provide a smooth, streamlined look and are often used in furniture and architectural components.
- Custom: For specialized applications, thin-walled aluminum tubes can be custom-formed into more complex shapes like L-sections, T-sections, and hexagonal profiles.
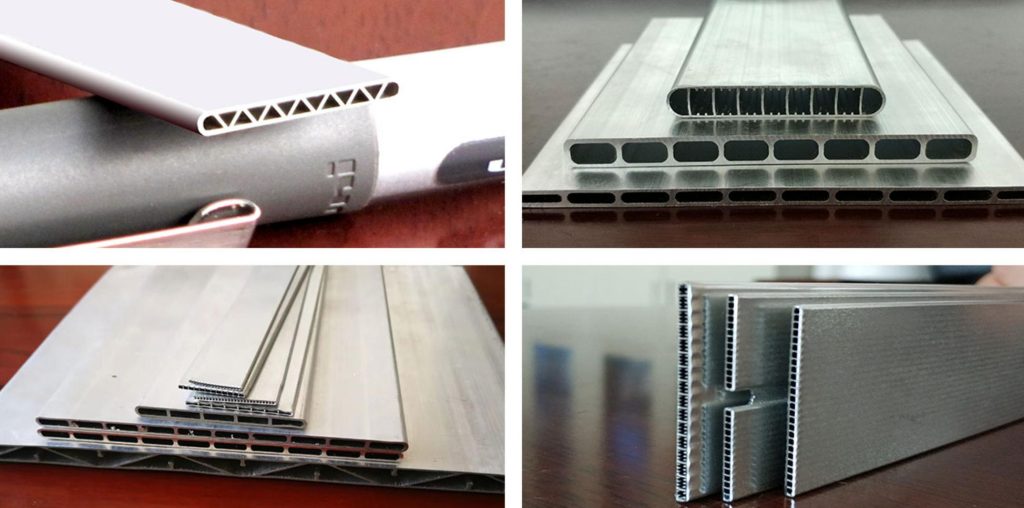
From Sizes:
- Diameter/width: Thin-walled aluminum tubes range in diameter or width from tiny micro-tubes (less than 1mm) to large tubes exceeding 12 inches.
- Wall thickness: The wall thickness is what defines “thin-walled,” typically ranging from 0.010 inches to 0.125 inches. It balances weight with strength and rigidity.
- Length: Tubes can be purchased in standard lengths (e.g., 10ft, 20ft) or cut to specific lengths depending on the application.
From Materials:
- Aluminum alloys: Different alloys offer varying degrees of strength, corrosion resistance, and weldability. Common choices include 6061, 6063, and 5052.
- Tempers: Temper refers to the heat treatment and affects the tube’s strength, ductility, and formability. Common tempers for thin-walled tubes are T4, T6, and H16.
What are the Benefits of Using Thin-Walled Aluminum Tubes in Different Applications?
The benefits of using thin-walled aluminum tubes in different applications are numerous and far-reaching. Here are some key advantages and recommended alloys for different applications:
Features | Benefits | Application Examples | Recommended Alloy |
Lightweight | Reduces weight, improves fuel efficiency and performance | Aerospace: Aircraft fuselages, wing structures, trusses, fuel tanks Automotive: Body panels, suspension components, engine parts Marine: Boat hulls, masts, railings | 6061, 7075, 5083 |
High Strength-to-Weight Ratio | Maintains strength despite thin walls | Construction: Trusses, frames, scaffolding Medical Implants: Orthopedic implants, prosthetic limbs Sports Equipment: Bicycle frames, ski poles, lacrosse sticks | 6061, 6063, 7075 |
Corrosion Resistance | Withstands rust and corrosion | Outdoor Furniture: Patio chairs, tables, benches Marine Equipment: Boat railings, fittings, ladders Building Components: Cladding, window frames, gutters | 6061, 5083, 5052 |
Good Conductivity | Efficiently conducts heat and electricity | Heat Sinks: Electronic components, LED lighting Electrical Components: Busbars, enclosures, cable trays HVAC Systems: Air ducts, heat exchangers | 6063, 5083, 3003 |
Machinability and Workability | Easy to cut, bend, and weld | Furniture: Frames, legs, supports Decorative Elements: Railings, light fixtures, signage Tubing: Plumbing, irrigation, handrails | 6061, 5052, 3003 |
Aesthetics | Attractive appearance, various finishes available | Architectural Accents: Façades, interior elements Consumer Products: Appliances, electronics, packaging Art and Design: Sculptures, installations, furniture | 6061, 5052, 6063 |
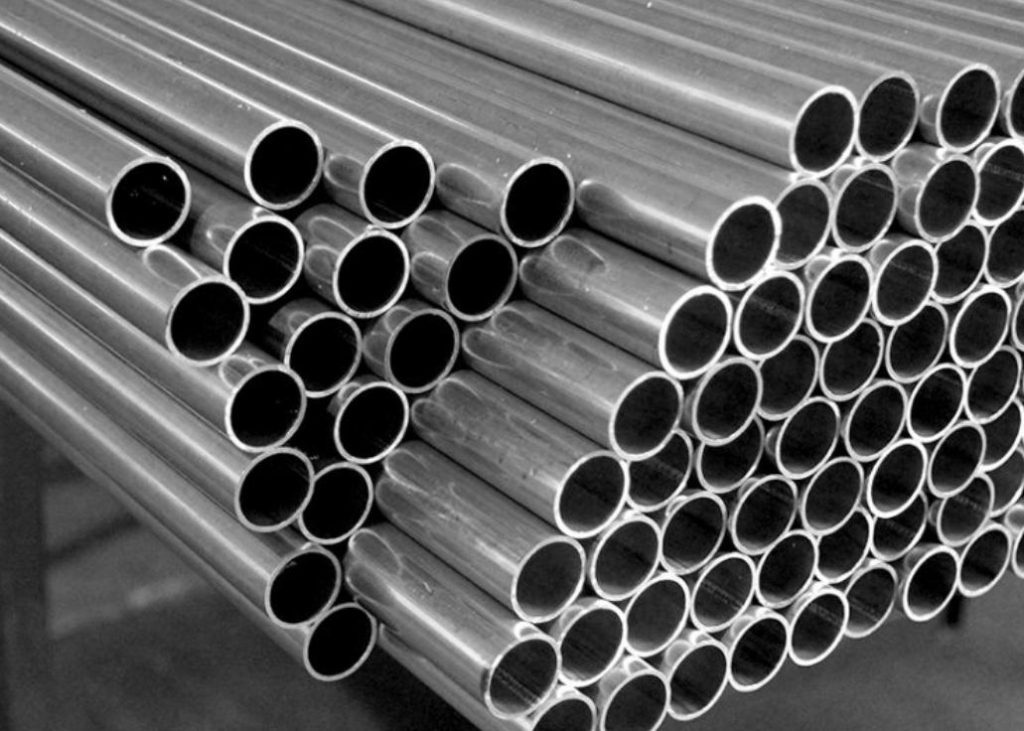
Conclusion:
Thin-walled aluminum tubes, in their unassuming strength and lightness, offer a glimpse into the future of materials engineering. They stand as a testament to human ingenuity, constantly evolving to meet new challenges and push the boundaries of what’s possible. As we strive for a lighter, more efficient world, these silent workhorses will continue to play a vital role, shaping everything from the vehicles we drive to the structures we inhabit. And should your own projects yearn for the magic of these slender giants, rest assured, a professional thin wall aluminum tubing supplier stands ready to equip your endeavors.