Welding 6061 T6 aluminum presents unique challenges and opportunities for welders across various industries. With its exceptional strength, lightweight nature, and corrosion resistance, 6061 T6 aluminum is a preferred choice for applications ranging from aerospace components to automotive parts and marine structures. However, achieving flawless welds with this aluminum alloy requires a deep understanding of its properties and the implementation of effective welding techniques. In this article, we’ll explore top tips and strategies for achieving flawless welds when working with 6061 T6 aluminum, ensuring the integrity and reliability of welded structures and components.
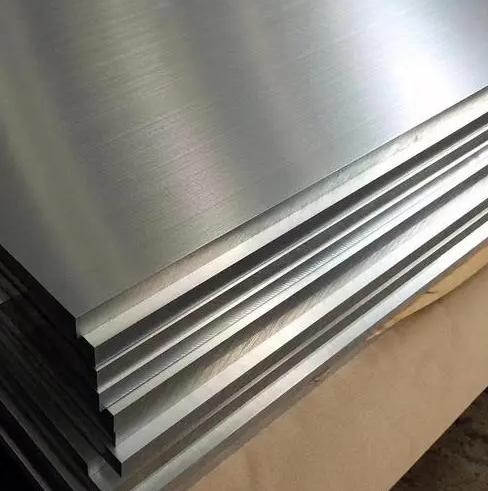
Why Choosing 6061 T6 Aluminum for Welding?
While 6061 T6 aluminum is a popular choice for various applications, including welding, it’s not necessarily the best option solely based on its weldability. Here’s a breakdown of the pros and cons, and why other options might be better suited for specific welding needs:
Pros of using 6061 T6 for welding:
- Decent weldability: Compared to some other aluminum series, particularly the 7000 series, 6061 T6 offers relatively good weldability. This means it can be joined using various welding processes with a lower risk of cracking.
- Availability: 6061 T6 is a widely available and affordable aluminum alloy, making it a convenient choice for many projects.
Cons of using 6061 T6 for welding:
- Susceptibility to cracking: Despite being considered “weldable,” 6061 T6 is still prone to cracking due to the presence of magnesium and silicon in its composition. This necessitates specific techniques and careful handling during the welding process to avoid these issues.
- Strength reduction: Welding can reduce the strength of 6061 T6 due to the heat involved. This might not be ideal for applications requiring high structural integrity.
Better alternatives for specific welding needs:
If weldability is the top priority, other series like the 5000 series (e.g., 5052) offer superior weldability with less risk of cracking and minimal strength reduction compared to 6061 T6.
Therefore, choosing the right aluminum alloy for welding should involve a comprehensive evaluation of the project’s specific requirements:
If weldability is paramount, explore alternatives like the 5000 series.
If other factors like availability and formability are more important, and you can manage the potential challenges associated with welding 6061 T6, then it might be a suitable choice.
Ultimately, the ideal selection depends on the unique demands of your specific welding project.
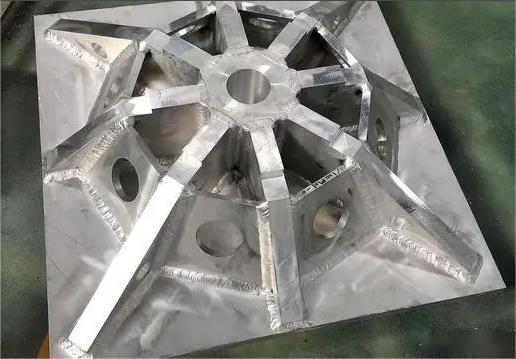
What are the Common Applications of Welding 6061 T6 Aluminum?
Despite the challenges associated with welding, 6061 T6 aluminum finds various applications due to its combination of properties:
General Applications:
Fabrication: 6061 T6 is commonly used in general fabrication projects due to its decent weldability, formability, and availability. This allows for the creation of various structures and components.
Repair: It can be used for repairing existing structures made from the same material, although careful handling is crucial to avoid introducing cracks.
Specific Applications:
- Automotive: 6061 T6 finds use in automotive components like frames, wheels, and engine parts. However, due to potential strength reduction after welding, its use is often limited to non-critical components.
- Marine: It can be used in non-structural marine applications like decks, railings, and some boat parts, where its corrosion resistance is beneficial. However, for critical structural components, other materials might be preferred.
- Building and Construction: Due to its strength and availability, 6061 T6 can be used in non-load-bearing building elements like cladding, frames, and decorative elements.
- Consumer Goods: It is found in various consumer goods, like electronics enclosures, sporting goods, and furniture, where its lightweight nature and aesthetic appeal are valued.
Key Points:
- While 6061 T6 offers decent weldability compared to some other aluminum series, it’s still susceptible to cracking and requires specific techniques for successful welding.
- Its strength can be reduced by welding, making it less suitable for applications requiring high structural integrity.
- When weldability is the top priority, other aluminum series might be better options.
Despite the challenges, the 6061 T6 remains a versatile choice for various applications due to its combination of properties.
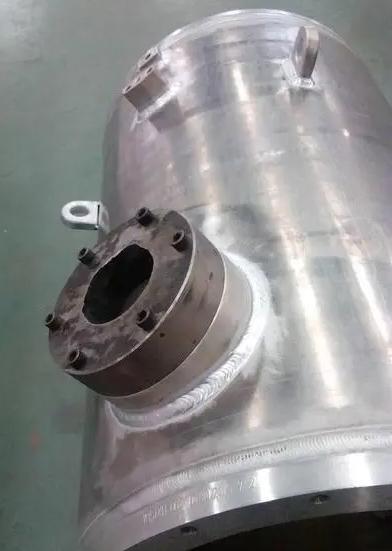
What are the Welding Techniques for 6061 T6 Aluminum?
While 6061 T6 presents some challenges for welding, several techniques can be employed to achieve successful and strong joints:
1. Gas Metal Arc Welding (GMAW) or MIG Welding:
- Widely used and versatile for welding 6061 T6. But requires using a filler metal (typically 5356 or 4043 alloy) to compensate for the magnesium burn-off during welding.
- Helium or argon shielding gas is used to protect the weld pool from contamination.
- Strict control of heat input is crucial to minimize the risk of cracking.
2. Tungsten Inert Gas Welding (TIG) or TIG Welding:
- Offers greater control and precision compared to MIG welding, making it suitable for thinner materials and critical applications.
- Does not require filler metal for autogenous welding (using the base metal itself to form the weld).
- Shielding gas is still necessary to protect the weld pool.
- Requires skilled operators due to the demanding technique.
3. Laser Beam Welding (LBW):
- Emerging technology offering highly concentrated heat input and deep penetration.
- Minimizes distortion and improves weld strength compared to conventional methods.
- Requires specialized equipment and skilled operators, making it less accessible for general applications.
Additional Considerations:
- Preheating: Heating the base metal (typically to 150-200°C) can improve weldability and reduce cracking risks.
- Post-weld heat treatment: In some cases, a controlled heating and cooling process after welding can help restore some of the lost strength in the heat-affected zone.
- Proper joint preparation: Cleaning and degreasing the joint area is crucial for optimal weld quality.
- Welding expertise: Regardless of the technique chosen, skilled and experienced welders are essential for achieving successful and safe welds with 6061 T6 aluminum.
Remember: Even with these techniques, 6061 T6 remains susceptible to cracking. It’s crucial to carefully assess your project’s requirements and consult with a qualified welding professional to determine the best approach and ensure successful results.
Conclusion
In conclusion, welding 6061 T6 aluminum demands precision, skill, and attention to detail. By implementing the top tips discussed in this article, welders can enhance their proficiency in welding this versatile aluminum alloy while minimizing common issues such as distortion, cracking, and porosity. From selecting the appropriate welding technique to optimizing welding parameters and ensuring proper joint preparation, every aspect of the welding process plays a crucial role in achieving flawless welds and maximizing the performance of welded aluminum structures and components. With continuous practice, learning, and adherence to best practices, welders can master the art of welding 6061 T6 aluminum and contribute to the production of high-quality, reliable products across diverse industries.