Aluminum strips are widely used across sectors such as construction, automotive, aerospace, and electronics. These strips come in various alloys, shapes, and finishes to suit specific functions and environments. Aluminum strips are divided into some categories according to the different classification standards, here are 5 common types of aluminum strips as follows:
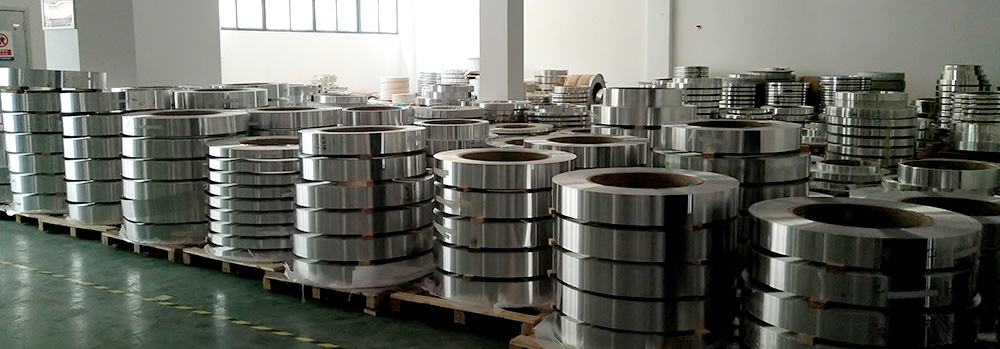
1. Classification by Alloy Composition
Aluminum strips are often classified by their alloy composition, which impacts the material’s strength, conductivity, corrosion resistance, and other key properties. Broadly, aluminum strips fall into two main categories based on alloy composition: pure aluminum strips and aluminum alloy strips.
Pure Aluminum Strips
- Composition: 99% or more aluminum content.
- Properties: Known for excellent corrosion resistance, high electrical and thermal conductivity, and low strength relative to alloys.
- Applications: Often used in electrical components, food packaging, and decorative applications. Specific uses include:
- Power Transmission Lines: Ideal for power lines and cables due to high conductivity.
- Food Containers: The corrosion-resistant properties make it suitable for food storage.
- Architectural Decoration: Used for trims, decorative panels, and other accents.
Aluminum Alloy Strips
- Composition: Aluminum combined with other metals like copper, zinc, magnesium, or manganese.
- Properties: Higher strength, better wear resistance, and greater corrosion resistance than pure aluminum.
- Applications: Preferred in industries that require durability and enhanced mechanical properties, such as aerospace, automotive, and construction. Alloy strips are divided into series based on the primary alloying element:
- 2000 Series (Aluminum-Copper Alloys): High strength, typically used in aerospace components.
- 3000 Series (Aluminum-Manganese Alloys): Moderate strength, commonly used in industrial goods.
- 4000 Series (Aluminum-Silicon Alloys): Good wear resistance, often applied in automotive parts.
- 5000 Series (Aluminum-Magnesium Alloys): Excellent seawater corrosion resistance, ideal for marine and coastal environments.
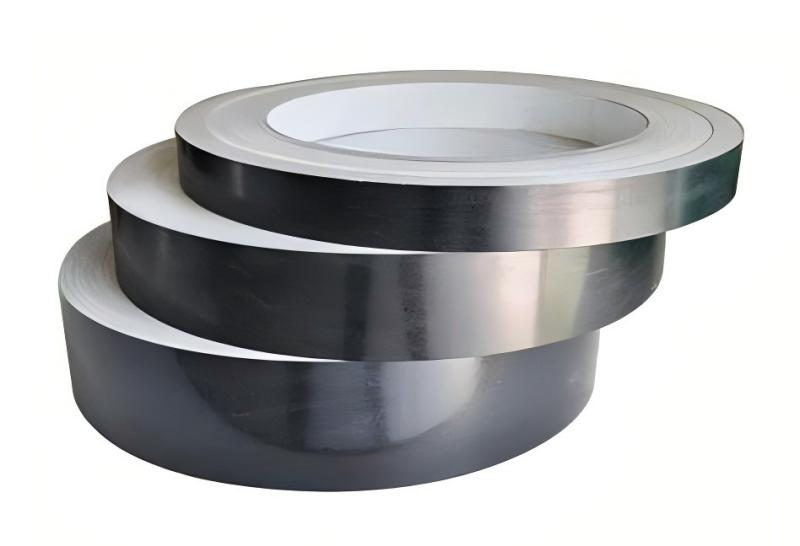
2. Classification by Physical Shape
Another way to classify aluminum strips is by their physical shape. Different shapes of aluminum strips offer varying advantages in terms of manufacturing ease, stability, and performance in specific applications.
Round Aluminum Strips
- Shape: Circular cross-section.
- Benefits: Simple manufacturing process, low cost, easy integration into rounded components.
- Applications: Used widely in aviation, automotive, and machinery for parts that require smooth, streamlined shapes, such as:
- Pipe Fittings: Round shape enables smooth fluid flow in plumbing and HVAC systems.
- Electrical Components: Shape helps in easy insulation and arrangement within circular housings.
Square Aluminum Strips
- Shape: Square cross-section.
- Benefits: Offers stability, and higher load-bearing capacity than round shapes.
- Applications: Commonly used in construction frameworks and furniture where stability is crucial, including:
- Structural Supports: Acts as framing in doors, windows, and walls.
- Furniture Manufacturing: Used as bases and supports, especially for load-bearing frames.
Hexagonal Aluminum Strips
- Shape: Hexagonal cross-section.
- Benefits: Excellent for torque transmission, unique shape adds aesthetic value.
- Applications: Preferred in machinery and architecture, especially where unique geometric shapes are beneficial, such as:
- Mechanical Parts: Shape aids in easy gripping and torque handling.
- Decorative Building Elements: Adds visual appeal to modern architectural designs.
3. Classification by Application
Aluminum strips can also be categorized by their intended applications, as their composition and physical properties make them suitable for a variety of specialized uses.
Construction Aluminum Strips
- Purpose: Used for structural support and decoration in buildings.
- Properties: High strength and corrosion resistance to withstand outdoor exposure.
- Applications:
- Door and Window Frames: Provide stability and durability.
- Curtain Walls: Used in modern facades for aesthetics and structural support.
Industrial Aluminum Strips
- Purpose: Essential in producing parts and components across aviation, automotive, electronics, and machinery.
- Properties: Enhanced strength, wear resistance, and corrosion resistance.
- Applications:
- Automotive Parts: Lightweight yet strong, suitable for body panels and structural elements.
- Machinery Components: Used in high-wear parts requiring durability.
Decorative Aluminum Strips
- Purpose: Adds aesthetic value to furniture and interior design.
- Properties: Treated surfaces for enhanced visual appeal and corrosion resistance.
- Applications:
- Furniture Edging: Adds a polished look to modern furniture.
- Interior Wall Panels: Decorative trims that provide sleek, contemporary finishes.
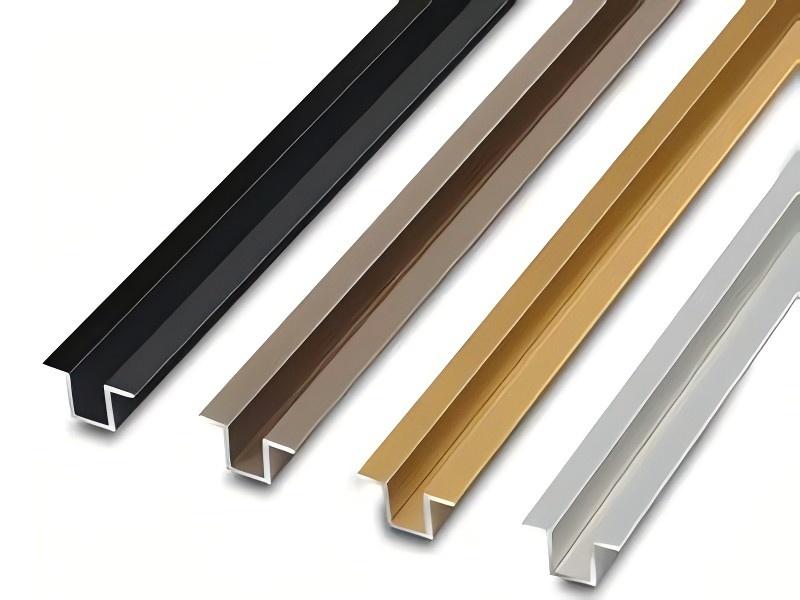
4. Classification by Surface Treatment
Surface treatment techniques add further value to aluminum strips by improving their durability, aesthetic qualities, and resistance to environmental wear.
Anodized Aluminum Strips
- Process: Anodization creates a porous oxide layer on the surface, which can be dyed.
- Benefits: Adds color, wear resistance, and corrosion protection.
- Applications:
- Decorative Panels: Available in various colors for architecture and interior design.
- Furniture: Common in handles, trims, and other accent pieces.
Electrophoretic Coating Aluminum Strips
- Process: An electric charge draws a uniform paint film onto the strip.
- Benefits: Provides high corrosion resistance and a smooth, polished finish.
- Applications:
- Architectural Trim: Used in window frames and structural accents.
- Furniture: Gives a glossy, durable finish for aesthetic appeal.
Powder-Coated Aluminum Strips
- Process: Powder coating covers the strip with a powder that is heated to create a strong, uniform layer.
- Benefits: Extremely durable, resistant to scratches and wear.
- Applications:
- Outdoor Furniture: Withstands weathering and retains color.
- Building Exteriors: Used in curtain walls and other decorative elements.
5. Classification by Specialized Use
Some aluminum strips are specifically engineered for particular applications, such as insulation, structural reinforcement, or decorative purposes.
Hollow Glass Aluminum Strips
- Purpose: Used in insulating glass for stability and sealant purposes.
- Types: Includes straight angle, angled, open, closed, and thermal bridge types.
- Applications:
- Insulating Glass Units: Helps maintain thermal insulation and structural integrity in double-pane windows.
- Sealing Frames: Creates airtight seals for better energy efficiency in buildings.
Decorative Trim Aluminum Strips
- Purpose: Used as finishing edges on paneling, doors, and carpets.
- Properties: Sleek, polished look with high durability.
- Applications:
- Furniture Edging: Provides clean edges for tables and cabinetry.
- Glass Door Tracks: Guides glass panels smoothly in sliding doors.
- Carpet Trimming: Provides polished, finished edges on carpet borders.
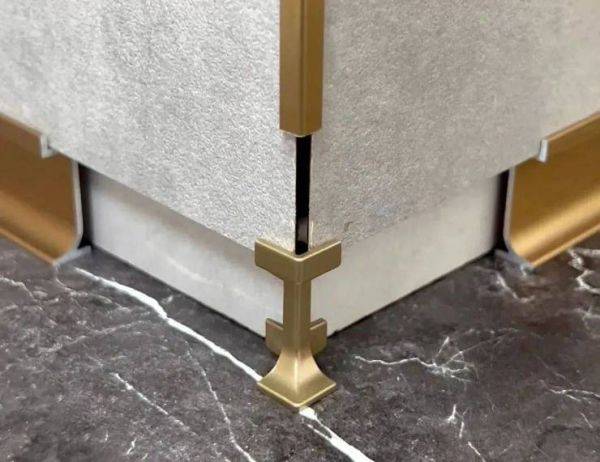
In summary, there are many types of aluminum strips, which can be divided into many types according to different classification standards. When choosing aluminum strips, the appropriate type of aluminum strips should be determined according to the specific application requirements and environmental conditions to ensure their performance and service life.