In the automotive industry, the pursuit of creating lighter, more fuel-efficient, and environmentally friendly vehicles has led to the increased use of aluminum in car bodies. Aluminum offers a unique combination of strength, durability, and lightness, making it an ideal material for modern car manufacturing. This article explores why aluminum is chosen for car bodies, the types of aluminum alloys used, the manufacturing processes involved, and how companies like CHAL supply high-quality aluminum for automotive applications.
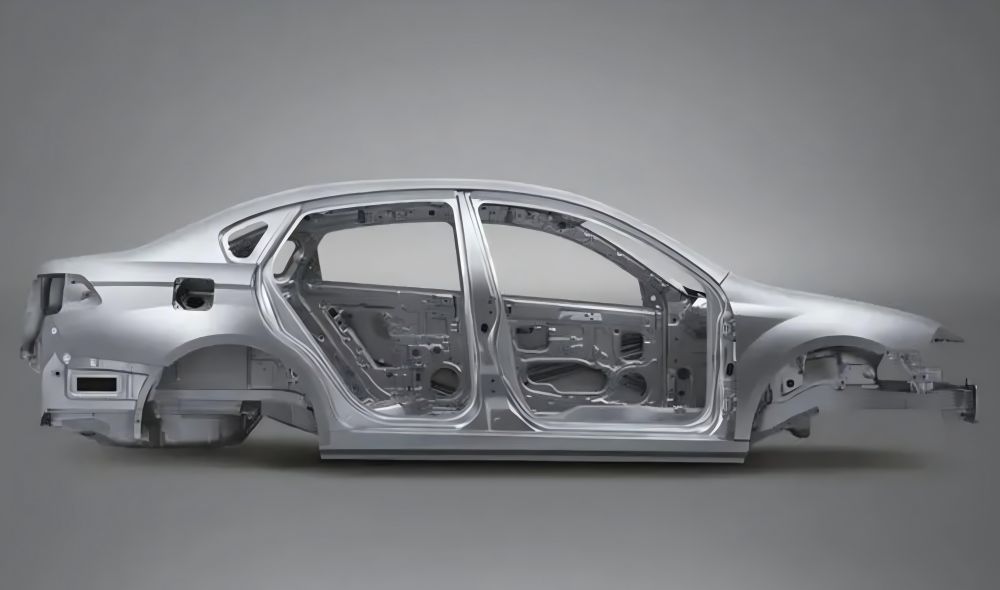
Why Aluminum is Ideal for Car Bodies?
The use of aluminum in the automotive industry dates back to the early 20th century, with the first notable example being the 1901 Durkopp sports car. However, it wasn’t until the latter half of the 20th century that aluminum began to be more widely adopted, primarily due to advancements in alloy technology and manufacturing processes. By the 1990s, car manufacturers such as Audi and Jaguar had started producing models with significant aluminum content, leading to widespread recognition of the material’s benefits.
Benefits of Using Aluminum in Car Bodies
Aluminum offers several benefits that make it ideal for car bodies:
- Lightweight: Aluminum is about one-third the weight of steel, which significantly reduces the overall weight of a vehicle. This reduction in weight translates to improved fuel efficiency and lower emissions, aligning with environmental regulations and consumer demand for eco-friendly vehicles.
- High Strength-to-Weight Ratio: Despite being lightweight, aluminum alloys possess high strength, providing the necessary structural integrity for car bodies while enhancing performance and handling.
- Corrosion Resistance: Aluminum naturally forms a protective oxide layer that prevents corrosion, ensuring the longevity and durability of car bodies, especially in harsh environmental conditions.
- Malleability and Formability: Aluminum can be easily formed into complex shapes, allowing for innovative design possibilities and the creation of sleek, aerodynamic car bodies.
- Recyclability: Aluminum is 100% recyclable without losing its properties, making it a sustainable choice that reduces the overall environmental impact of vehicle production.
In conclusion, the historical adoption and the multitude of benefits associated with aluminum make it a cornerstone material in the evolution of car manufacturing.
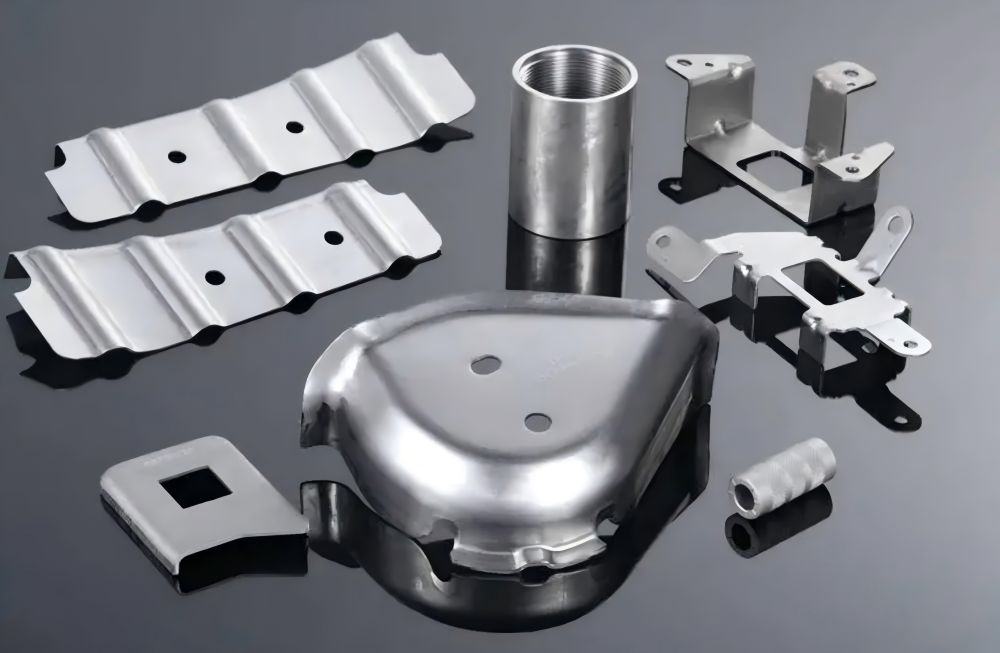
What is the Aluminum for the Car Body?
As the automotive industry continues to innovate and evolve, the materials used in car manufacturing play a crucial role in defining the performance, safety, and efficiency of vehicles. Aluminum has emerged as a pivotal material for car bodies, offering a perfect balance of strength, lightness, and versatility. This section delves into the specific types of aluminum alloys utilized in car bodies, the sophisticated manufacturing processes involved, and the challenges and considerations that manufacturers must address.
Types of Aluminum Alloys Used in Car Bodies
Several types of aluminum alloys are used in car bodies, each with distinct properties tailored to specific applications:
- 5000 Series Alloys: These are high-magnesium alloys known for their excellent corrosion resistance and moderate strength. They are often used in structural components and outer panels. Common alloys like 5083 and 5182.
- 6000 Series Alloys: These alloys, containing magnesium and silicon, are known for their good mechanical properties and corrosion resistance. They are commonly used in body panels, bumpers, and structural reinforcements. Common alloys like 6061 and 6063.
- 7000 Series Alloys: These are high-strength alloys containing zinc and are primarily used in high-stress components due to their exceptional strength and toughness. Common alloys like 7075 and 7050.
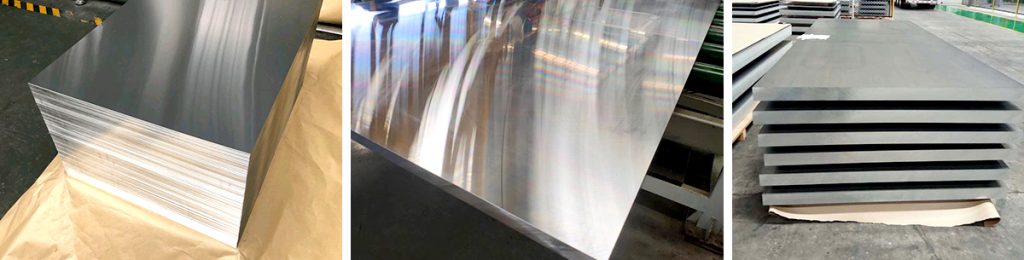
Manufacturing Processes for Aluminum Car Bodies
The manufacturing processes for aluminum car bodies include:
- Sheet Metal Forming: This involves the shaping of aluminum sheets into car body parts using techniques such as stamping, rolling, and deep drawing. Sheet metal forming is widely used for creating exterior panels and structural components.
- Extrusion: In this process, aluminum is forced through a die to create long, straight shapes such as beams and supports. Extrusion allows for the production of complex cross-sectional profiles used in structural and reinforcement components.
- Casting: Casting involves pouring molten aluminum into molds to create parts with intricate shapes. This method is often used for engine blocks, transmission cases, and other complex components.
- Joining Techniques: Various joining techniques are employed to assemble aluminum components, including welding, adhesive bonding, and riveting. Each method has its advantages depending on the application and desired strength of the joint.
Challenges and Considerations
While aluminum offers numerous advantages, its implementation in car bodies also presents challenges:
- Cost: Aluminum is generally more expensive than steel, which can impact the overall cost of vehicle production.
- Manufacturing Complexity: Working with aluminum requires specialized equipment and techniques, which can increase manufacturing complexity and require additional training for workers.
- Material Fatigue and Durability: Although aluminum is resistant to corrosion, it can be susceptible to fatigue and stress fractures over time, particularly in high-stress applications. Careful design and engineering are necessary to mitigate these risks.
In conclusion, understanding the types of aluminum alloys, the manufacturing processes involved, and the challenges associated with aluminum car bodies is crucial for leveraging this material effectively in automotive design and production.
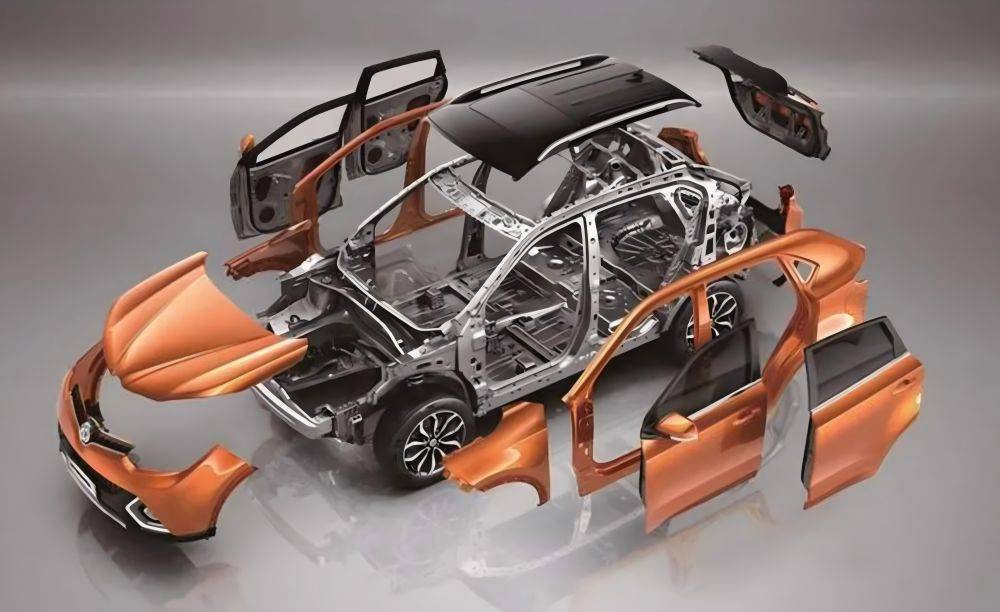
Get Aluminum for the Car Body From CHAL
For car manufacturers seeking high-quality aluminum for their vehicles, CHAL is a leading supplier offering a wide range of aluminum materials for many applications including automotive. CHAL provides:
- Diverse Alloy Selection: CHAL offers a variety of aluminum alloys, including 5000, 6000, and 7000 series, ensuring the right material for every component of the car body.
- Advanced Manufacturing Capabilities: With state-of-the-art manufacturing facilities, CHAL can provide aluminum materials (including tubes, sheets, plates, profiles, etc.) for different processes such as extrusion, casting, and sheet metal forming.
- Quality Assurance: CHAL adheres to stringent quality control standards to ensure the reliability and performance of their aluminum products, meeting the demands of the automotive industry.
- Sustainable Practices: Committed to environmental sustainability, CHAL employs eco-friendly manufacturing practices and emphasizes the recyclability of aluminum, contributing to greener automotive production.
In conclusion, CHAL stands out as a reliable partner for automotive manufacturers, providing high-quality aluminum solutions that enhance vehicle performance, efficiency, and sustainability. If you are looking for an automotive aluminum supplier, please feel free to contact CHAL.