Concrete is one of the most widely used construction materials globally, thanks to its durability, versatility, and strength. Over the years, various additives and admixtures have been introduced to enhance its properties and performance. One such additive is aluminum powder. Here we explore the processes involved in using aluminum powder in concrete and its various impacts on the material’s properties and the environment. Additionally, we also recommend you a reliable supplier of aluminum powder.
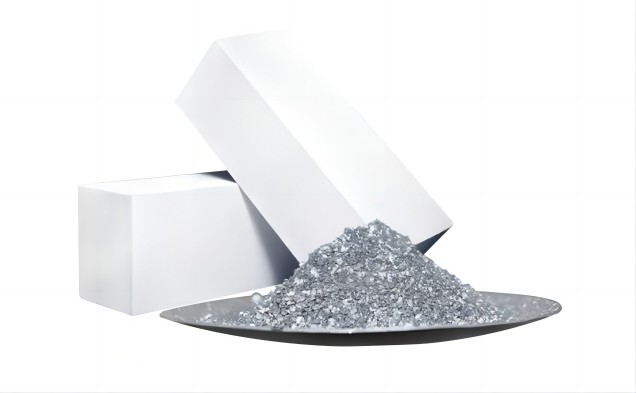
Understanding Aluminum Powder in Concrete
Aluminum powder is primarily used in concrete to produce lightweight aerated concrete, commonly known as autoclaved aerated concrete (AAC) or cellular concrete. When mixed with water and cement, aluminum powder reacts with the alkaline components in the mixture, releasing hydrogen gas. This gas forms tiny, evenly distributed bubbles within the concrete, creating a porous structure. The resulting material is significantly lighter than traditional concrete while maintaining considerable strength and insulating properties.
Different Types of Concrete and Suitable Aluminum Powder
Before diving into specific types, it’s essential to grasp the fundamental interaction between concrete and aluminum powder.
Aluminum powder reacts with the alkaline environment of concrete, producing hydrogen gas. This gas creates tiny bubbles within the concrete matrix, resulting in a lighter, more insulating material.
The type of aluminum powder used significantly influences the properties of the resulting concrete. Factors like particle size, purity, and reactivity determine the rate of gas production and the final characteristics of the concrete.
Type of Concrete | Description | Suitable Aluminum Powder |
Autoclaved Aerated Concrete (AAC) | Lightweight, precast concrete providing excellent thermal insulation and sound absorption | Fine aluminum powder with particle sizes from 10 to 45 microns for uniform distribution and consistent reaction |
Non-Autoclaved Aerated Concrete (NAAC) | Similar to AAC but cured under normal atmospheric conditions | Slightly coarser aluminum powder with particle sizes from 20 to 60 microns for adequate aeration under ambient conditions |
Foamed Concrete | Highly flowable, lightweight material used for void filling, insulation layers, and trench reinstatement | Aluminum powder with particle sizes from 10 to 100 microns, chosen based on desired density and bubble size |
Lightweight Aggregate Concrete | Uses lightweight aggregates along with aluminum powder to reduce overall weight while maintaining strength | Moderate particle size aluminum powder, ranging from 20 to 50 microns, to complement the lightweight aggregates |
Gas Concrete | Air-entrained concrete improving workability, reducing bleeding, and enhancing freeze-thaw durability | Fine aluminum powder with particle sizes between 5 to 25 microns for creating small, uniformly distributed gas bubbles |
Selection Criteria for Aluminum Powder:
- Particle Size: The particle size of the aluminum powder significantly affects the aeration process. Fine powders produce smaller bubbles and a more uniform pore structure, while coarser powders create larger bubbles and a more porous structure.
- Purity: High-purity aluminum powder ensures consistent reactions and prevents impurities from affecting the concrete’s properties.
- Reactivity: The aluminum powder should have a controlled reactivity with the alkaline components in the concrete mix to ensure predictable aeration and bubble formation.
- Consistency: Consistent particle size distribution and reactivity are crucial for achieving uniform properties in the final concrete product.
Different types of aerated concrete benefit from specific types of aluminum powder tailored to their unique requirements. Understanding the role of particle size, purity, reactivity, and consistency helps in selecting the appropriate aluminum powder for each application.

Processes of Aluminum Powder and Concrete Mixing
Incorporating aluminum powder into concrete involves several critical steps to ensure proper mixing, aeration, and curing. Here’s a detailed outline of the process:
1. Preparation of Ingredients
- Cement: The primary binding material.
- Sand: Fine aggregate for the concrete mix.
- Water: Essential for the hydration of cement and reaction with aluminum powder.
- Aluminum Powder: The key additive for creating aerated concrete.
Measurement: Accurately measure the proportions of each ingredient. The amount of aluminum powder typically ranges from 0.05% to 0.2% of the cement weight, depending on the desired aeration and concrete type.
2. Mixing
- Dry Mixing: Combine the dry ingredients—cement, sand, and aluminum powder. Ensure thorough mixing to distribute the aluminum powder evenly throughout the mixture.
- Adding Water: Gradually add water while continuously mixing. The water initiates the hydration of the cement and the reaction of the aluminum powder with the alkaline components.
- Control Mixing: Maintain a controlled mixing environment to prevent excessive foaming or premature reactions. The consistency of the mix should be monitored to ensure it meets the desired specifications.
3. Casting and Molding
- Pouring: Once the mixture reaches the desired consistency, pour it into molds. The choice of molds depends on the intended application of the concrete.
- Leveling: Ensure the mix is evenly distributed within the molds and leveled properly to avoid any irregularities in the final product.
4. Aeration Reaction
- Chemical Reaction: The aluminum powder reacts with the alkaline components (calcium hydroxide) in the cement-water mixture, releasing hydrogen gas.
- Bubble Formation: The released hydrogen gas forms tiny bubbles throughout the concrete mix, creating a porous structure. This process needs to be carefully controlled to achieve uniform bubble distribution.
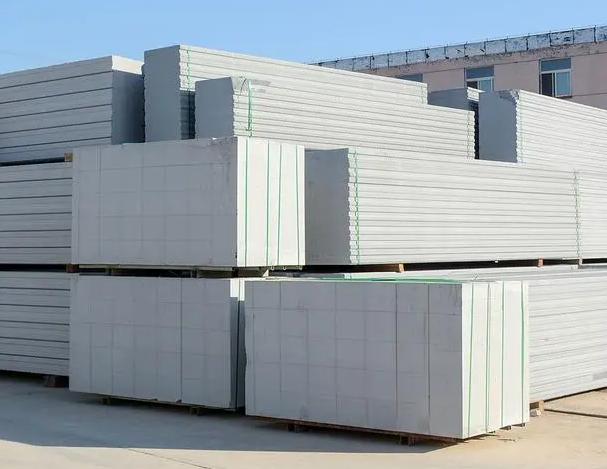
5. Curing
Autoclaved Aerated Concrete (AAC):
- Autoclaving: Place the molds in an autoclave, a pressure vessel that subjects the concrete to high temperature and pressure. This accelerates the curing process and enhances the strength and durability of the concrete.
- Curing Time: Typically ranges from 8 to 12 hours, depending on the specific requirements and autoclave settings.
Non-Autoclaved Aerated Concrete (NAAC) and Foamed Concrete:
- Ambient Curing: Allow the concrete to cure under normal atmospheric conditions. The curing time can vary from a few days to several weeks, depending on the type of concrete and environmental conditions.
- Moisture Maintenance: Keep the concrete moist during the curing process to ensure proper hydration and strength development.
6. Finishing and Quality Control
- Demolding: Carefully remove the cured concrete from the molds. Ensure the concrete has achieved sufficient strength to withstand handling.
- Quality Inspection: Inspect the finished product for any defects, such as uneven aeration, cracks, or incomplete curing. Perform necessary quality control tests to verify the properties of the concrete.
- Surface Treatment: Apply any required surface treatments, such as smoothing or coating, to enhance the concrete’s appearance and performance.
Incorporating aluminum powder into concrete is a meticulous process that requires careful preparation, mixing, casting, and curing. By following these steps and maintaining strict quality control, construction professionals can produce high-quality aerated concrete with the desired properties and performance characteristics. Properly incorporating aluminum powder not only enhances the concrete’s physical properties but also contributes to more efficient and sustainable construction practices.
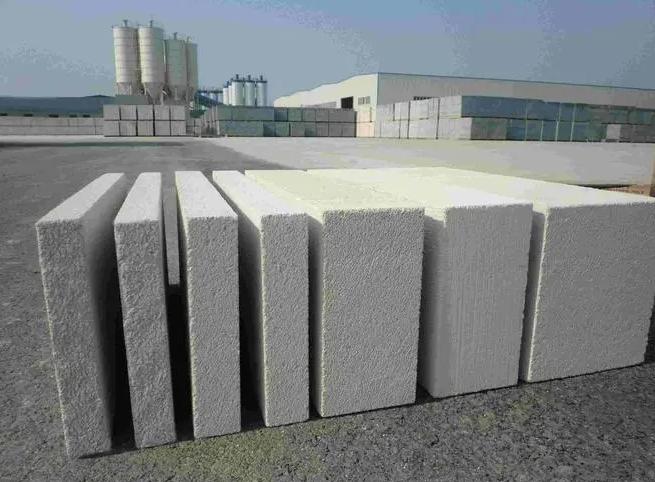
Impacts of Using Aluminum Powder in Concrete
Impact on Concrete Properties
- Density Reduction: Aluminum powder significantly reduces the density of concrete, creating a lightweight material. This is particularly advantageous for reducing the overall load on structures and simplifying transportation and handling.
- Thermal Insulation: The porous structure of aerated concrete provides excellent thermal insulation. The trapped air pockets within the concrete reduce heat transfer, contributing to energy efficiency in buildings by reducing heating and cooling demands.
- Sound Insulation: The air pockets formed by the aluminum powder also enhance sound insulation properties. Aerated concrete effectively dampens sound transmission, making it ideal for applications where noise reduction is important, such as residential and commercial buildings.
- Ease of Handling: Lightweight concrete is easier to cut, shape, and install. This enhanced workability allows for greater flexibility in design and construction, reducing labor costs and construction time.
- Strength Maintenance: Despite being lighter, aerated concrete maintains considerable compressive strength. While it may not match the strength of traditional concrete, it is sufficient for many structural and non-structural applications, including walls, floors, and roofing panels.
Environmental Impacts
- Reduced Material Usage: The lightweight nature of aerated concrete means less raw material is required for construction, leading to resource conservation.
- Energy Efficiency: Improved thermal insulation properties contribute to energy savings in buildings, reducing heating and cooling costs.
- Sustainability: The production of aluminum powder and aerated concrete can be environmentally friendly if sourced and manufactured responsibly, minimizing carbon footprint and promoting sustainable construction practices.
Looking for High-Quality Aluminum Powder Supplier
The use of aluminum powder in concrete presents numerous advantages, including improved workability, reduced weight, and enhanced thermal properties. For achieving the best results in concrete applications, sourcing high-quality aluminum powder is crucial. CHAL is a trusted supplier of aluminum products, offering premium-grade aluminum powder suitable for various types of aerated concrete.
Why Choose CHAL?
- Quality Assurance: CHAL ensures that the aluminum powder meets stringent quality standards, providing consistency and reliability in performance.
- Technical Support: CHAL offers expert guidance on the appropriate use of aluminum powder in different concrete applications, helping customers achieve optimal results.
- Competitive Pricing: CHAL provides high-quality products at competitive prices, ensuring cost-effectiveness for large-scale projects.
- Sustainable Practices: CHAL is committed to environmentally responsible manufacturing processes, aligning with sustainable construction goals.
To procure high-quality aluminum powder for your concrete projects, visit CHAL’s website or contact their sales team for detailed product information and support.