Aluminium for cars, to put it simply, refers to aluminum and aluminum alloy materials used in the automobile manufacturing process. With the development of the modern automobile industry, higher requirements have been put forward for automobile performance, safety, fuel economy, and environmental protection. Due to its unique physical and chemical properties, aluminum has gradually become an indispensable material in automobile manufacturing.
In the early days of automobile development, traditional materials such as steel were mainly used. However, with the advancement of technology, the advantages of aluminum have gradually become prominent. It has a low density, which can effectively reduce the weight of the car, and also has good strength, machinability, and corrosion resistance. Today, aluminum is widely used in automobiles, from engine parts to body frames to interior parts.
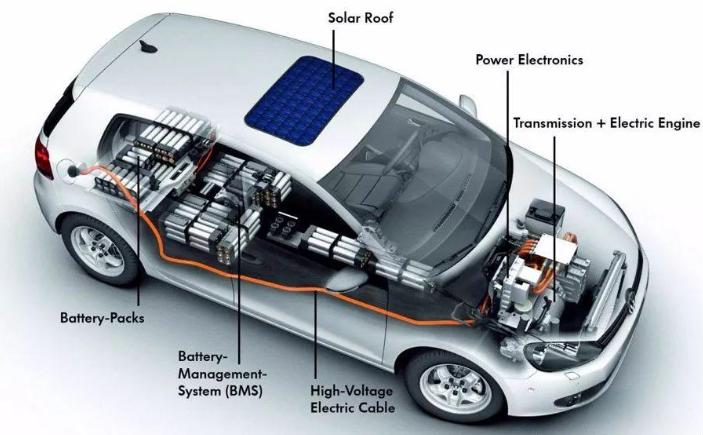
Types of Aluminium Used in Cars
Not all aluminium is created equal. In the automotive industry, various types of aluminium alloys are tailored to meet specific performance and design needs. These alloys are categorized based on their composition and properties, making them suitable for diverse applications.
1000 series aluminum (industrial pure aluminum)
1000 series aluminum is the series with the highest aluminum content, with a purity of more than 99.00%. It has good electrical conductivity, thermal conductivity and corrosion resistance, but its strength is relatively low.
It is mainly used in some parts with high electrical conductivity requirements in automobiles, such as automotive wires and cables. Due to its corrosion resistance, it can also be used for some simple decorative parts of automotive interiors, such as the substrate of some interior strips.
2000 series aluminum (mainly copper-aluminum alloy)
The copper element in 2000 series aluminum gives it high strength, and its mechanical properties can be further improved by heat treatment, but its corrosion resistance is relatively poor.
It is often used in some high-strength parts of automobile engines, such as the piston of the engine. The piston needs to withstand high temperature, high pressure, and high-speed friction during the operation of the engine, and the 2000 series aluminum can meet its strength requirements.
3000 series aluminum (manganese-aluminum alloy)
3000 series aluminum improves the strength and corrosion resistance of aluminum alloys by adding manganese elements and has good formability.
3000 series aluminum is often used in automotive cooling system components, such as automotive radiators. Radiators require good heat dissipation performance as well as certain strength and corrosion resistance, and 3000 series aluminum meets these requirements.
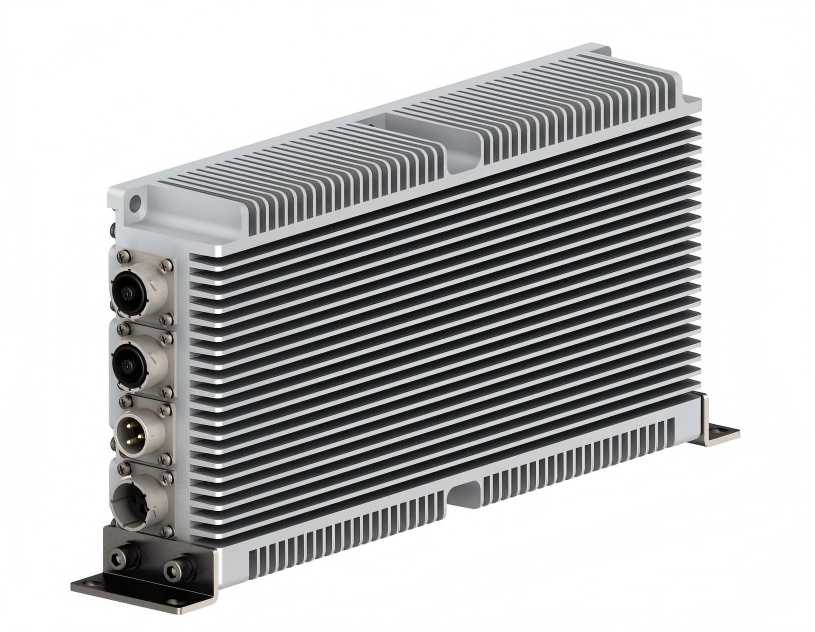
4000 series aluminum (silicon aluminum alloy)
The silicon element in 4000 series aluminum improves the casting performance of aluminum alloy, making it have good fluidity, easy to cast parts of complex shapes, and good stability at high temperatures.
The engine block is a typical application component of 4000 series aluminum. The engine block has a complex structure and needs to work stably at high temperatures. The casting performance and high temperature stability of 4000 series aluminum make it an ideal material for manufacturing cylinder blocks.
5000 series aluminum (magnesium aluminum alloy)
5000 series aluminum is added with magnesium and has medium strength, good corrosion resistance, and weldability.
It is used in automobile body frames and body panels. The body frame requires a certain strength and good corrosion resistance. 5000 series aluminum can reduce the weight of the body while ensuring the overall strength of the body, and resisting corrosion from the external environment. The use of 5000 series aluminum for body panels also helps reduce the weight of the vehicle.
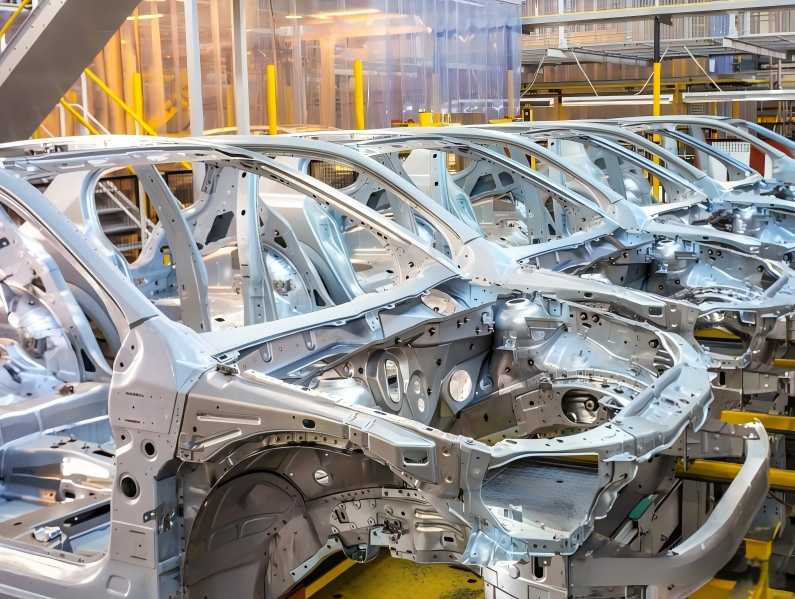
6000 series aluminum (magnesium silicon aluminum alloy)
6000 series aluminum is a heat-treatable aluminum alloy with good comprehensive properties, including high strength, good corrosion resistance and machinability.
6000 series aluminum is often used in the door and window frames of automobiles. Door and window frames need to have a certain strength to ensure safety, and at the same time have good corrosion resistance and machinability. 6000 series aluminum can meet these requirements well.
7000 series aluminum (zinc aluminum alloy)
The zinc element in 7000 series aluminum gives it extremely high strength. It is one of the strongest series of aluminum alloys, but its corrosion resistance is relatively weak, and special surface treatment is usually required.
It is used in some key parts of the car that have extremely high strength requirements, such as the suspension system parts of the car. The suspension system is under great stress during the driving process of the car, and 7000 series aluminum can provide sufficient strength to ensure the reliability of the suspension system.
Different grades of aluminum play their own unique roles in different parts of the car, and together they contribute to the goals of optimizing car performance, ensuring safety and lightweighting.
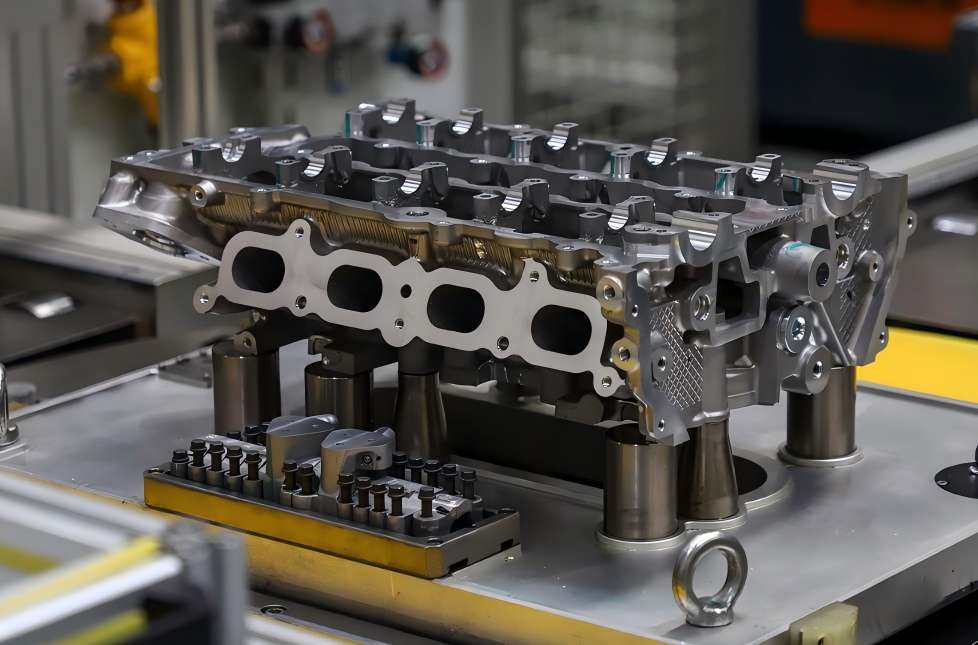
Benefits of automotive aluminum
The widespread adoption of aluminium in cars is driven by its ability to address some of the industry’s most pressing challenges, including fuel efficiency, performance optimization, and being highly recyclable.
Lightweight advantage
The lightweight advantage of automotive aluminum plays a significant role in improving the vehicle’s fuel economy (traditional fuel vehicles) and battery range (electric vehicles). It also helps improve the vehicle’s handling performance.
The density of aluminum is about 2.7g/cm³, which is significantly lower than that of steel (density is about 7.8g/cm³). This property allows the use of aluminum in automobile manufacturing to significantly reduce vehicle weight. Taking the body frame as an example, if aluminum alloy materials are used instead of traditional steel materials, a significant weight reduction can be achieved. In traditional fuel vehicles, for every 100 kilograms of vehicle weight reduction, fuel consumption can be reduced by approximately 0.3 to 0.6 liters per 100 kilometers. For electric vehicles, weight reduction is directly related to the improvement of battery range, helping to reduce battery energy consumption and thus extend the vehicle’s driving range.
Performance improvement
Automotive aluminum excels in improving performance. Its high strength-to-weight ratio, good corrosion resistance, and thermal conductivity help improve the safety, durability, and overall performance of cars.
- High strength to weight ratio: Although aluminum has a low density, it has a high strength to weight ratio. With the right alloying and processing techniques, aluminum alloys can achieve strength levels comparable to or even higher than some steel materials. For example, some high-strength aluminum alloys are used in key structural components of automobiles, such as body frames and suspension system components. While ensuring that these components have sufficient strength to ensure vehicle safety, they can also bring about other performance improvements due to weight reduction.
- Good corrosion resistance: Aluminum will naturally form a dense protective film of aluminum oxide in the air. This film can effectively prevent further oxidation and corrosion of aluminum. In the automotive environment, aluminum parts are better able to resist corrosion, whether it is humid climate conditions or salt erosion on the road (such as roads with salt and snow in winter). Compared with steel parts, aluminum body parts do not require frequent anti-rust treatment, which not only reduces maintenance costs but also extends the service life of the car.
- Good thermal conductivity: Aluminum has good thermal conductivity, which is of great significance in the cooling system of automobiles. For example, automobile radiators are made of aluminum, which can quickly dissipate the heat generated by the engine and ensure that the engine operates at a suitable temperature, thereby improving the engine’s working efficiency and reducing the risk of failure caused by overheating.
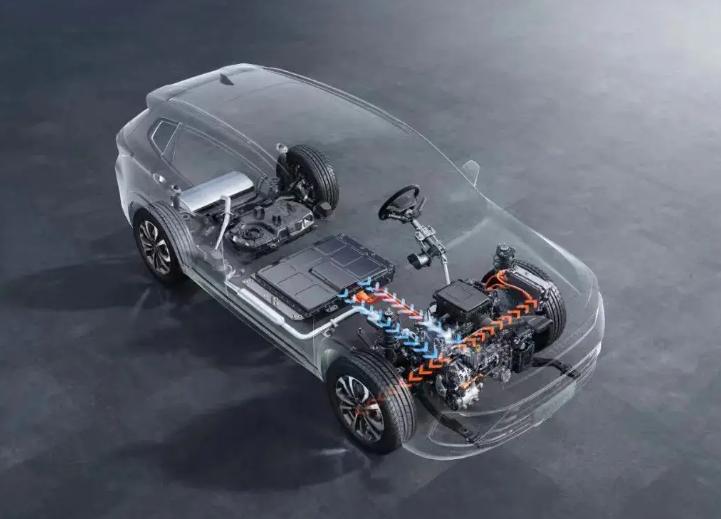
Recycling Value
Aluminum has a high recycling value. After a car is scrapped, its aluminum parts can be easily recycled and reused. Compared with refining aluminum from aluminum ore, the process of recycling aluminum consumes significantly less energy, only 5% to 10% of the energy consumed in primary aluminum production. Moreover, recycled aluminum can be reprocessed into various automotive parts or other aluminum products, ensuring performance while achieving resource recycling, which is in line with the concept of sustainable development.
Design Flexibility
Aluminum has strong machinability and can adapt well to processing processes such as casting, rolling, or extrusion. This gives automotive designers greater flexibility when designing vehicle styling and structure. For example, aluminum profiles with complex shapes and high precision requirements can be manufactured through the extrusion process for use in body frames or interior structural components. In terms of car exterior design, aluminum body panels can more easily achieve complex curved surface shapes to meet the aesthetic and aerodynamic design requirements of modern cars.
By offering weight savings, performance enhancements, and environmental benefits, aluminium has become an essential material for sustainable and innovative car manufacturing.
Processing Technology of Aluminium for Automobiles
The journey of aluminium from raw material to automotive components involves advanced processing technologies. These methods are critical in ensuring aluminium meets the stringent requirements of modern vehicles.
- Casting: Die-casting and sand-casting are the most common methods. Used for complex shapes like engine blocks and cylinder heads.
- Extrusion: Produces lightweight yet strong components like crash management systems and roof rails. Enables the creation of hollow or solid profiles with precise dimensions.
- Sheet Forming: Aluminium sheets are stamped and formed into body panels. But requires advanced techniques to handle aluminium’s lower ductility compared to steel.
- Joining Techniques: Includes riveting, adhesive bonding, and friction stir welding to assemble aluminium components. Also need to overcome challenges related to aluminium’s lower weldability.
Innovative processing technologies ensure that aluminium meets the automotive industry’s high standards for quality, performance, and efficiency.
In conclusion, aluminium has emerged as a transformative material in car manufacturing, offering a blend of lightweight efficiency, strength, and sustainability. From high-performance sports cars to eco-friendly EVs, aluminium is paving the way for innovation in the automotive industry. As technology continues to evolve, its potential to enhance vehicle design, performance, and environmental impact remains unparalleled.