Aluminum tubes are indispensable components in a wide range of industries, valued for their versatility, durability, and lightweight properties. Whether used in aerospace, construction, automotive manufacturing, or a host of other applications, the selection of the right aluminum tube is a decision that profoundly impacts both project performance and budgetary constraints. In this article, we delve into the intricacies of aluminum tube cost, explore the multifaceted factors that influence pricing, and then guide you through the art of choosing the perfect aluminum alloy to meet your specific application requirements.
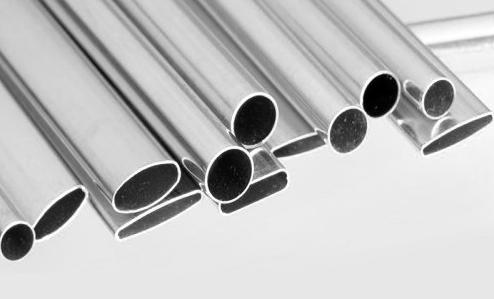
11 Factors Affecting Aluminum Tube Cost
1. Aluminum Alloy Type
One of the primary factors influencing the cost of aluminum tubes is the choice of alloy. Aluminum alloys vary in composition and properties, and they can significantly impact the final cost. Common alloys like 6061 and 6063 are often more affordable than specialized or high-strength alloys such as 7075. The selection of the alloy should align with the specific needs of the application, balancing performance requirements and cost constraints.
2. Tube Dimensions
The size and dimensions of the aluminum tube play a vital role in determining its cost. Larger diameter tubes and those with thicker walls require more raw material, resulting in higher manufacturing and material costs. Smaller tubes with standard dimensions are generally more cost-effective. Engineers and project managers should carefully evaluate the required tube dimensions to strike the right balance between performance and cost.
3. Production Quantity
Economies of scale come into play when considering production quantity. Larger production runs often reduce the per-unit cost of aluminum tubes. Manufacturers can optimize their processes, reduce setup times, and achieve better material utilization with larger orders. Conversely, smaller quantities may incur higher production costs due to these inefficiencies.
4. Customization and Fabrication
Custom features and complex fabrication requirements can significantly impact the cost of aluminum tubes. Drilling, bending, welding, and other specialized processes add labor and machining costs. Engineers must carefully assess whether such customization is essential for the application or if standardized tubes would suffice, thus reducing overall project costs.
5. Surface Finish
The desired surface finish of the aluminum tube is another cost factor. Additional treatments like anodizing, powder coating, or polished finishes enhance aesthetics and durability but can increase the overall cost. The choice of surface finish should align with the application’s functional and aesthetic requirements while staying within budget constraints.
6. Tolerance and Precision
Applications with tight tolerances and high precision requirements may drive up the cost of aluminum tubes. Achieving precise dimensions and straightness can be more labor-intensive and may involve additional quality control measures. Balancing the need for precision with budget considerations is crucial for cost-effective outcomes.
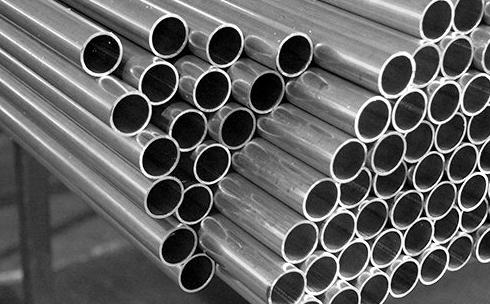
7. Length
The length of the aluminum tube directly affects material consumption and production processes. Longer tubes require more raw material and may necessitate special handling during production and transportation. Evaluating whether shorter or standard lengths can fulfill the application’s requirements without compromising structural integrity is essential for cost optimization.
8. Market Demand and Price Fluctuations
The aluminum market is subject to supply and demand fluctuations, impacting raw material costs. Prices can vary based on market conditions, so timing procurement can influence the overall cost. Project managers should monitor market trends and plan accordingly to capitalize on favorable pricing opportunities.
9. Certifications and Compliance
Certain applications, such as those in the aerospace or automotive sectors, may require compliance with industry-specific certifications and standards (e.g., ASTM, ISO). Meeting these requirements often involves additional testing, documentation, and quality control measures, which can affect the cost.
10. Waste and Scrap
The efficiency of the manufacturing process can impact the amount of waste and scrap generated. Minimizing waste through optimized cutting and machining processes can help control costs. Additionally, recycling scrap aluminum can contribute to cost savings and sustainability efforts.
11. Packaging and Shipping
The cost of packaging and shipping should not be overlooked, especially for bulk orders or oversized aluminum tubes. Efficient packaging and logistics can help reduce these costs while ensuring the safe delivery of materials to the project site.
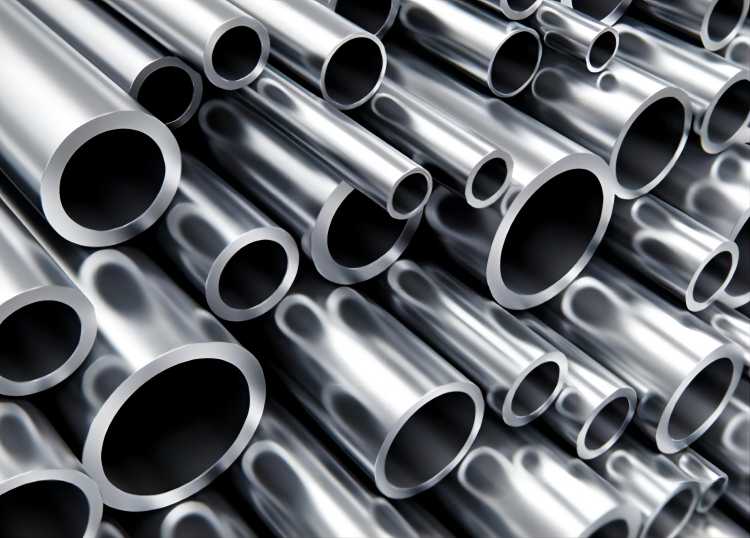
How to Choose the Right Aluminum Tube for Specific Applications?
Choosing the right aluminum tube for specific applications involves considering the unique requirements and constraints of each application. Here are some examples of specific applications and guidelines for selecting the appropriate aluminum tube:
Application | Key Considerations | Recommended Aluminum Alloy(s) |
Aerospace | Weight, high strength | 7075, 2024 |
Automotive Components | Strength, weight, corrosion resistance | 6061, 6063 |
Heat Exchangers | Thermal conductivity, corrosion resistance | 3003, 6061 |
Marine Applications | Corrosion resistance, durability | 5086, 5083 |
Structural Frameworks | Strength, durability, formability | 6061, 6063 |
Electrical Conduits | Electrical conductivity, corrosion resistance | 6061-T6 |
Pneumatic Systems | Strength, lightweight | 6061, 6063 |
Bicycle Frames | Lightweight, durability, ride quality | 7005, 6061 |
Architectural Applications | Aesthetics, corrosion resistance | 6063 |
Food and Beverage Industry | Hygiene, corrosion resistance, ease of cleaning | 6061, 3003 |
Medical Equipment | Lightweight, durability, corrosion resistance | 6061, 7005 |
DIY Projects | Ease of handling, availability | 6061 |
Conclusion
In summary, the journey from contemplating the costs of aluminum tubes to the selection of the optimal aluminum alloy for your project is a nuanced and intricate process. As you set out on this path, bear in mind that a well-informed decision not only guarantees cost-efficiency but also ensures top-notch performance and long-lasting durability. By evaluating aspects such as the alloy variant, tube dimensions, production volume, customization, and adherence to industry standards, you can confidently navigate the complexities of procuring aluminum tubes from manufacturers. Equipped with this knowledge, you are well-positioned to make choices that not only enhance your budgetary efficiency but also elevate the overall success of your project, whether it takes flight in the skies, traverses the highways, or shapes the world around us.