Aluminum, the second most widely used metal globally, plays a pivotal role in the refrigeration industry due to its lightweight nature, corrosion resistance, and high thermal conductivity. From household refrigerators to industrial cold storage systems, aluminum drives technological advancements by enhancing heat exchange efficiency and reducing energy consumption. This article explores aluminum’s material properties, applications, advantages, and challenges in refrigeration systems.
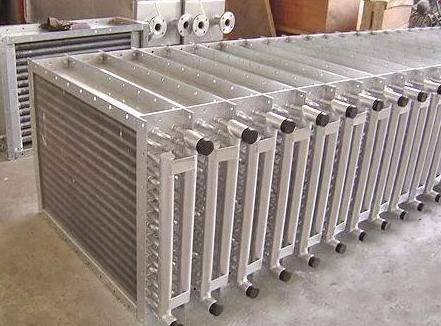
Aluminum Properties Relevant to Refrigeration
Aluminum’s unique physicochemical characteristics make it ideal for refrigeration applications:
- High Thermal Conductivity: Aluminum’s thermal conductivity (237 W/m·K) is ~60% of copper’s, but its density (2.7 g/cm³) is only one-third of copper’s, offering superior mass-specific heat transfer efficiency.
- Corrosion Resistance: Alloying (e.g., with Mn or Mg) and surface treatments (e.g., anodizing) enable aluminum to withstand refrigerants (e.g., R134a) and condensate. For example, 3003 aluminum alloy exhibits 40% better salt spray resistance than pure aluminum.
- Manufacturing Flexibility: Aluminum can be extruded or stamped into complex geometries, such as microchannel heat exchanger tubes with wall thicknesses as low as 0.2 mm—unachievable with copper.
Aluminum’s lightweight and thermal efficiency makes it a preferred alternative to copper and steel. However, alloy selection must align with specific operational demands, such as corrosion resistance and mechanical strength.
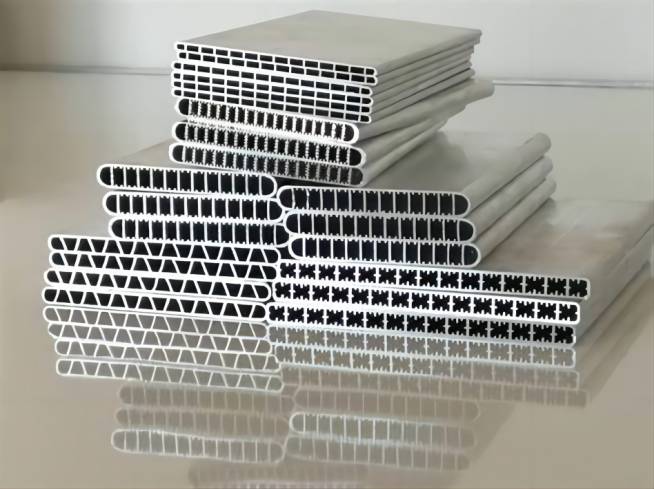
Applications of Aluminum in Refrigeration Systems
Aluminum accounts for over 60% of material usage in modern refrigeration systems, spanning four critical areas:
Heat Exchangers
Aluminum is extensively used in evaporators and condensers, the core components of heat exchangers. Its high thermal conductivity allows for efficient heat transfer between the refrigerant and the surrounding air or fluid. Aluminum fins and tubes maximize the surface area for heat exchange, further enhancing performance. Microchannel heat exchangers, which utilize small aluminum tubes, have gained popularity in automotive and HVAC systems due to their compact design and high efficiency.
Tubing Systems
Aluminum tubing is used for refrigerant lines due to its corrosion resistance and formability, increasingly replacing traditional copper tubes in refrigeration systems. It provides a reliable and leak-free pathway for the refrigerant throughout the system. Its lightweight nature reduces the overall weight of the system, especially advantageous in large installations. For example, in commercial air conditioning units, aluminum tubes are used to transport refrigerants with minimal risk of leakage.
Structural Components
The lightweight and strong nature of aluminum makes it ideal for constructing frames and panels for refrigeration units. In portable refrigeration units, such as those used in logistics, aluminum reduces the weight while maintaining structural durability. In refrigerated display cases and storage units, aluminum provides a clean and aesthetically pleasing surface.
Refrigeration Appliances
From household refrigerators to commercial freezers, from refrigerator walls to internal shelves, aluminum is widely used in various refrigeration appliances. Its properties contribute to energy efficiency, durability, and cost-effectiveness. The usage of Aluminum increases longevity of devices. Additionally, aluminum’s ability to reflect heat makes it suitable for insulated panels.
Overall, aluminum’s versatile properties make it an indispensable material in a wide range of refrigeration applications, enhancing efficiency, durability, and sustainability.
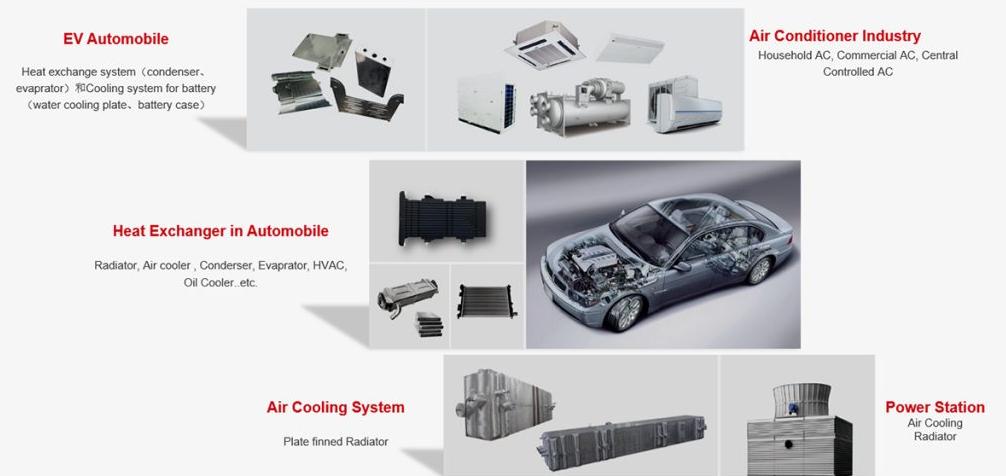
Advantages and Challenges
Advantages of Using Aluminum in Refrigeration
The use of aluminum in refrigeration systems offers several benefits:
- Energy Efficiency: High thermal conductivity ensures rapid heat transfer, reducing energy consumption.
- Cost-Effectiveness: Aluminum is generally more affordable than copper, making it an economical choice.
- Lightweight: Aluminum components reduce the overall weight of refrigeration systems, which is particularly beneficial for transportable and portable units.
- Durability: Corrosion resistance and structural integrity enhance the longevity of refrigeration equipment.
- Sustainability: The recyclability of aluminum aligns with global efforts to reduce environmental impact.
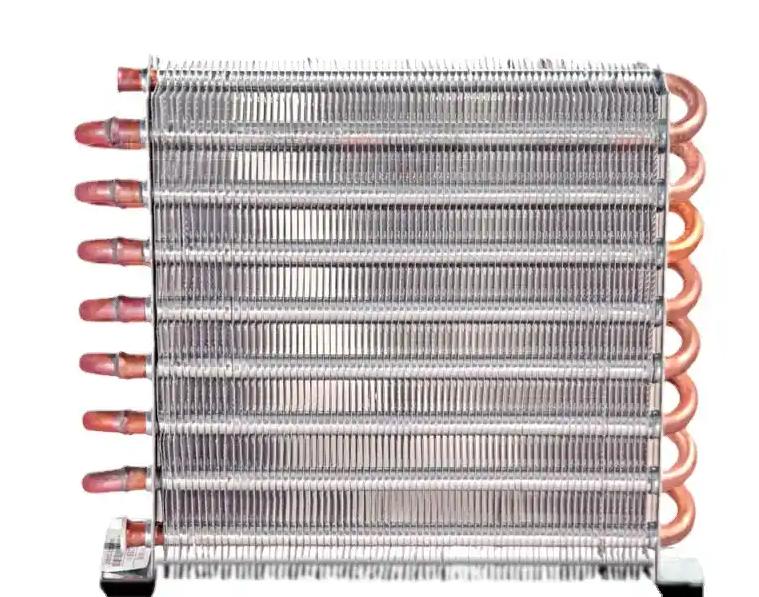
Challenges and Considerations
While aluminum offers many advantages, it also presents certain challenges:
- Lower Thermal Conductivity Compared to Copper: Copper remains the preferred choice in high-performance systems requiring maximum heat transfer efficiency.
- Potential for Galvanic Corrosion: When aluminum is paired with other metals, such as copper, galvanic corrosion may occur, requiring careful design and protective measures.
- Strength Limitations in High-Stress Applications: In some cases, aluminum’s lower tensile strength compared to other metals may limit its use in high-pressure systems.
- Fabrication Challenges: Specialized welding and joining techniques may be required, increasing manufacturing complexity.
Despite these challenges, advancements in alloy development and protective coatings are addressing many of these limitations, expanding the scope of aluminum’s applications.
Aluminum is redefining refrigeration materials, with proven success in residential, commercial, and industrial applications. Emerging technologies like microchannel systems and hybrid welding promise expanded use in ultra-low-temperature (-80°C) cooling and aerospace thermal management. However, enhancing corrosion resistance and establishing industry standards remain critical. Through collaborative R&D, aluminum could boost refrigeration system COP by 30%, accelerating global decarbonization efforts.