Anodizing and electroplating are two common surface treatment methods for aluminum material processing. What’s the difference between them? Which processing method is better? After reading this article in 5 minutes, you will know the difference.
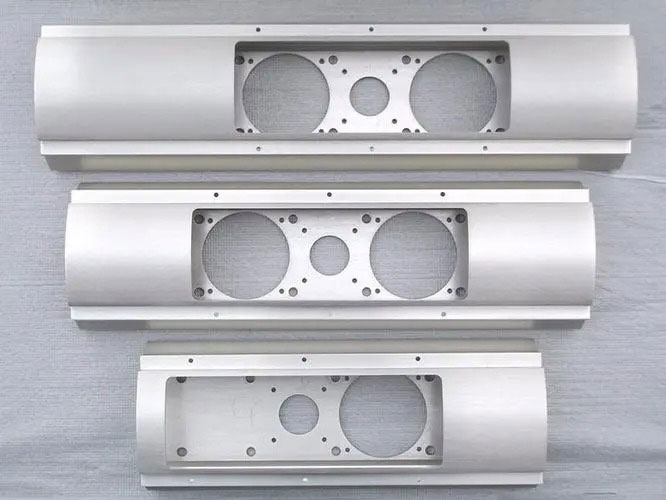
What is anodizing of aluminum?
Anodizing of aluminum refers to a material protection technology that uses aluminum as an anode in an acidic electrolyte to produce an oxide film on the surface of aluminum through electrolysis.
There are various electrolytes for the anodization of aluminum, but they are formulated with sulfuric acid, chromic acid, oxalic acid, or boric acid as the main component. Among them, the most commonly used ones are sulfate-based. The power supply can be direct current, alternating current, or alternating direct current. The voltage is between 5 and 25 volts, and the temperature is below 25°C.
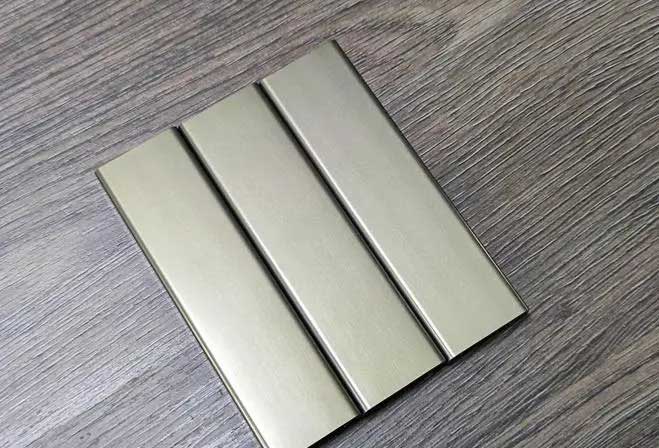
Through anodizing treatment, the surface of the metal material can be given a beautiful appearance, good corrosion resistance, wear resistance, insulation, and other functions, to meet different design requirements.
At present, the most widely used is the anodization of aluminum. Because the oxide film of aluminum has a fine structure, good adsorption, and is not easy to fall off, a fine oxide film is plated by the anodizing process to protect it from continuous oxidation.
There are many anodizing processes for aluminum materials, including ordinary anodizing, hard anodizing, and ultra-low temperature hard anodizing. In particular, hard anodizing is widely used in pistons, cylinders, cylinder linings, hydraulic presses and turbines, steam valves, gears, firearm parts, clutches, brake discs, and other hard wear-resistant and corrosion-resistant aluminum alloy parts on the surface treatment.
What is the electroplating treatment of aluminum?
Aluminum has the advantages of good electrical conductivity, fast heat transfer, light-specific gravity, and easy forming.
Therefore, in order to promote strengths and avoid weaknesses, electroplating is used to solve this problem in modern industry.
The advantage of aluminum electroplating is that it can improve the decorative properties of aluminum materials. Improve the surface hardness and wear resistance of aluminum materials such as aluminum plates, reduce friction coefficient, and improve lubricity. Improve the electrical conductivity of the aluminum wire surface. Improve corrosion resistance (including combination with other metals), ease of welding, improve bonding force with the rubber when hot-pressed, improve light reflectivity and repair dimensional tolerances of aluminum materials.
All kinds of metal substrates and some non-metallic materials can be electroplated as long as they undergo reasonable pretreatment (for example, ordinary leaves can also be electroplated with reasonable pretreatment).
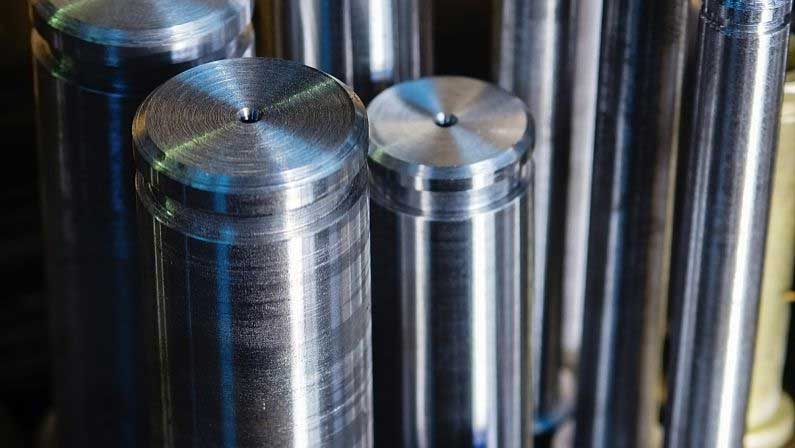
Different from anodic oxidation, electroplating uses the material to be plated as the cathode, the same metal material as the coating metal is used as the anode (insoluble anode is also used), and the electrolyte is a solution containing the metal ions of the coating; the input between the anode and the cathode is certain. After the current, due to the effect of charge, the metal anode ions move to the cathode and get electrons at the cathode, and deposit on the material to be plated.
Should we choose anodizing or electroplating?
At present, the most widely used is the anodization of aluminum. Because the oxide film of aluminum has a fine structure, good adsorption, and is not easy to fall off, a fine oxide film is plated by the anodizing process to protect it from continuous oxidation.
But if you need aluminum with good looks or excellent electrical conductivity, anodized aluminum is your better choice.
It is often said that the fit is the best. Therefore, when choosing electroplating or anodizing as the surface treatment of aluminum, you should choose a suitable surface treatment method according to your needs.