The prebaked anode is the most critical part of the electrolytic processing of aluminum, and it plays an important role in the electrolysis of aluminum. In this paper, the influence of the anode structure and height on the aluminum electrolysis process will be introduced by the prebaked anode.
Analysis of the influence of prebaked anode structure on the aluminum electrolysis process:
Influence of slotted anode on temperature field of the aluminum electrolysis cell.
First, the slotted anode can improve the flow of the electrolyte to a certain extent, which in turn has a certain effect on the temperature of the electrolytic cell. The temperature in the middle of the electrolytic cell is high and the temperature in the periphery is low, which is very beneficial to the outer crust.
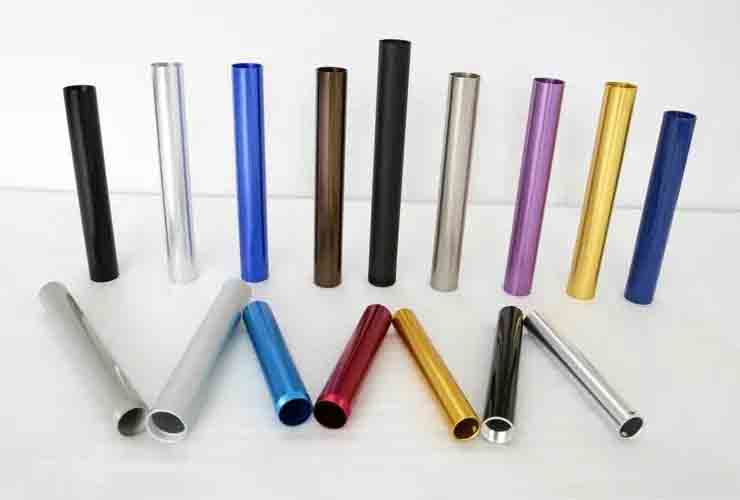
Second, improve the solubility of alumina and reduce the generation of precipitation. After the anode is slotted, part of the high-temperature and high-heat electrolyte will flow into the inside of the electrolytic cell, which will combine with the lower temperature alumina, causing a certain change in the temperature field in the middle of the electrolytic cell and accelerating the dissolution rate of alumina;
Third, the heat dissipation state at the bottom of the anode is effectively improved, which is very beneficial to the heat balance inside the electrolytic cell.
The influence of the slotted anode on the anode process is mainly as follows:
1) Effectively reduce anode overvoltage and save energy;
2) Reduce the actual current density of the anode and reduce the occurrence of the anode effect;
3) Reduce the probability of secondary reactions and effectively improve the current efficiency;
4) The slotted anode has a great influence on the anode process and the electrolysis process, which can greatly reduce the negative impact of the current on the anode process and promote the stable operation of the electrolysis cell.
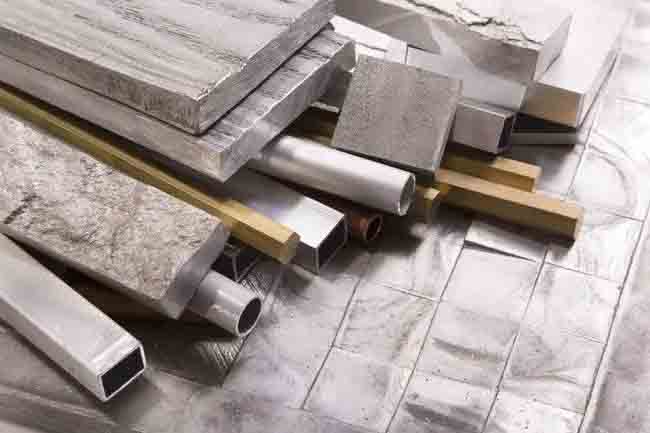
Effect of Prebaked Anode Height on Aluminum Electrolysis Process
The height of the prebaked anode will have a great influence on the anode voltage drop, DC power consumption, and anode consumption of the aluminum electrolytic cell.
In addition, the choice of anode height is quickly limited by anode production equipment, electrolytic cell structure, thermal balance conditions, etc. Therefore, in the process of aluminum electrolysis, the choice of anode height is very critical.
The experimental results show that the increase of the anode height will increase the voltage of the anode, and the DC power consumption of aluminum electrolysis will also increase, thus affecting the technical and economic indicators of the electrolytic cell. The above change trend can be verified by calculation.
Assume that the daily anode consumption of the electrolytic cell is 15mm, and the design cell voltage is 4200mV. The calculation shows that the DC power consumption of the anode tank with the anode height of 550mm is 14000 kWh/ton of aluminum.
The DC power consumption of an anode cell with an anode height of 590mm is 14,000 degrees per ton of aluminum. The consumption of 14050 degrees per ton of aluminum increases the production cost of electrolytic aluminum.
However, increasing the height of the anode cell can reduce the total consumption of aluminum electrolysis anodes. Since there are fewer corresponding remaining electrodes, the number of anode assemblies is reduced, thereby reducing the production cost of electrolytic aluminum.
By comparing the laboratory performance of two prebaked anodes with different heights, it can be found that, within a certain range, if the technical parameters of the electrolytic cell design are not changed, the increase of the prebaked anode height will improve the economics of the prebaked anode.
Therefore, in the later stage of the electrolytic cell design process, the economic benefits of aluminum electrolysis can be improved by appropriately increasing the height of the prebaked anode.
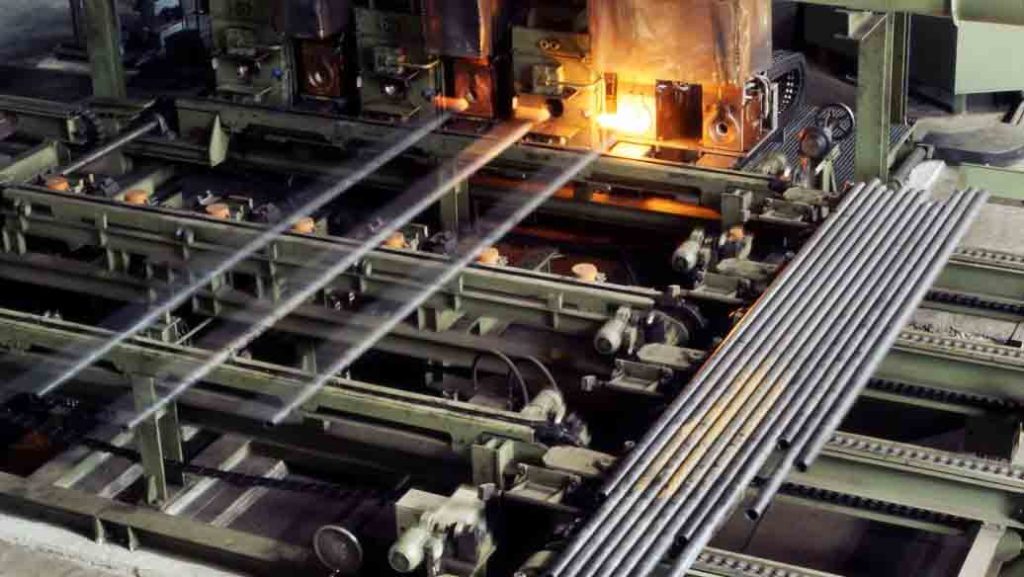
Influence of prebaked anode perforation on aluminum electrolysis process
The prebaked anode perforation is to open a plurality of vertical air holes at the bottom of the anode, and these air holes all penetrate the anode.
This structure can reduce the work done by the viscous force of the liquid electrolyte fluid that the CO2 bubbles need to overcome during the overflow process so that the gas can be discharged in time, thereby effectively reducing the thickness of the bubble layer at the bottom of the anode and the infiltration distance of the bubbles. Pole distance, to create conditions for reducing power consumption per ton of aluminum.
The application of perforated anodes can significantly reduce the direct current consumption per ton of aluminum, which can greatly improve the economic benefits of enterprises.
Effect of Anode Lengthening of Prebaked Aluminum Electrolytic Cell on Aluminum Electrolysis Process
1) It is theoretically feasible to lengthen the anode without changing the cell structure, and its main technical parameters do not change much;
2) After the anode is lengthened, the pole changing period can be extended by about 3d, which can reduce the pole changing workload of workers in industrial production to a certain extent and improve the stability of the electrolytic cell.
3) After the anode is lengthened, the anode current density is reduced, the temperature of the tank shell is reduced, the furnace side is thickened, the amount of carbon residue is reduced, the effect coefficient is reduced, the redness of the tank shell is reduced, and the side leakage accident is reduced.
Summarize
The prebaked anode is the most critical part of the aluminum electrolysis cell and plays a critical role in the whole electrolysis production process. Anode slotting, increasing anode height and length, and anode perforation can all improve the economic and technical indicators of the aluminum electrolysis process to a certain extent.
In the production process, the relevant staff must fully understand the influence of the length, slotting method, height, perforation, and other factors of the prebaked anode on the production of electrolytic aluminum, and make necessary technical parameter adjustments to improve the efficiency of aluminum electrolysis. Current efficiency, reduced power consumption, and improve efficiency of aluminum electrolysis.