Autoclaved Aerated Concrete (AAC) blocks have become a staple in modern construction due to their lightweight nature, excellent thermal insulation, and soundproofing qualities. These blocks owe much of their advantageous properties to aluminum powder, a crucial component in their manufacturing process. This article delves into the role of aluminum powder for AAC block, its impact on block quality, methods for controlling its usage, and the significance of its purity.
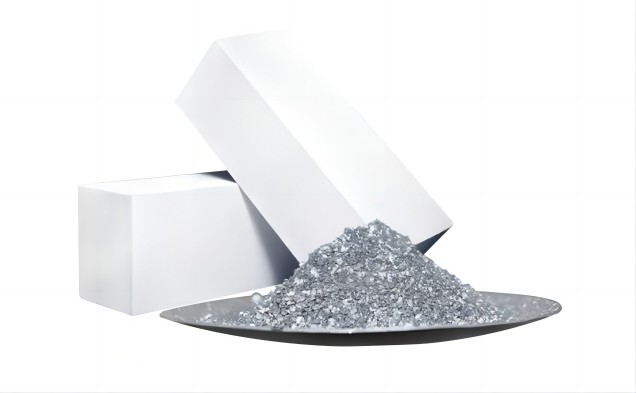
Aluminum Powder and Its Role in AAC Blocks
Aluminum powder serves as a gas-forming agent in the production of AAC blocks. When aluminum powder is mixed with alkaline substances like lime and cement, a chemical reaction occurs that produces hydrogen gas. This gas creates tiny bubbles within the concrete slurry, resulting in a porous structure as the mixture sets and cures. These pores are integral to the lightweight nature of AAC blocks, providing both thermal insulation and soundproofing.
The reaction can be summarized as follows:
2Al+3Ca(OH)2+6H2O→3CaO·Al2O3·6H2O+3H2
This process not only reduces the overall density of the material but also enhances its insulation properties. The efficiency of this gas-forming reaction is pivotal to the quality of the final product, making the careful control of aluminum powder usage essential in AAC block manufacturing.
Impact of Aluminum Powder Quantity on AAC Block Quality
The amount of aluminum powder used in the AAC block production process directly influences the final product’s characteristics.
- Dry Density: The amount of aluminum powder used directly affects the dry density of AAC blocks. An increase in aluminum powder leads to the formation of more hydrogen gas, creating more pores and reducing the material’s overall density. This reduction in density is beneficial for the lightweight characteristic of AAC blocks, making them easier to handle and reducing the load on structural elements.
- Compressive Strength: The quantity of aluminum powder also significantly impacts the compressive strength of AAC blocks. When used in optimal amounts, aluminum powder helps achieve a balance between pore formation and structural integrity. However, excessive aluminum powder can result in oversized or unevenly distributed pores, weakening the material and reducing its compressive strength. Therefore, achieving the right balance in aluminum powder usage is crucial for maintaining the structural performance of AAC blocks.
- Thermal and Acoustic Insulation: The porous structure created by aluminum powder enhances the thermal and acoustic insulation properties of AAC blocks. The air pockets within the material act as barriers to heat transfer and sound propagation, making AAC blocks excellent insulators. Proper control of aluminum powder ensures the formation of a uniform pore structure, maximizing these insulation benefits.

Methods for Controlling Aluminum Powder Usage in AAC Block Production
The amount of aluminum powder used in the production process of autoclaved aerated concrete (AAC) blocks has a decisive impact on the quality and performance of the final product. Controlling the amount of aluminum powder is a key step in ensuring that AAC blocks have appropriate porosity and mechanical strength.
- Precise Measurement: Accurate dosing equipment is essential for controlling the amount of aluminum powder added to the AAC mix. Precise measurement ensures that each batch of product meets the desired density and strength specifications.
- Raw Material Ratio Adjustment: The proportion of aluminum powder needs to be adjusted based on the types and qualities of other raw materials used. Different silica and calcareous materials react differently with aluminum powder, necessitating careful optimization of the mix.
- Mixing and Gas Formation Control: Uniform mixing of aluminum powder with other raw materials is vital for consistent gas formation. The mixing time and speed must be controlled to ensure thorough integration and efficient reaction.
- Environmental Condition Monitoring: Temperature and humidity in the production environment can affect the reaction rate and the resulting pore structure. Real-time monitoring and adjustment of these conditions are crucial for maintaining product quality.
- Production Process Optimization: Continuous improvement of the production process, such as optimizing the pouring and curing stages, can enhance aluminum powder utilization and ensure even pore distribution.
- Quality Testing and Feedback: Regular quality testing, including checks for density, strength, and porosity, provides feedback for adjusting aluminum powder usage. This closed-loop control system helps maintain consistent product quality.
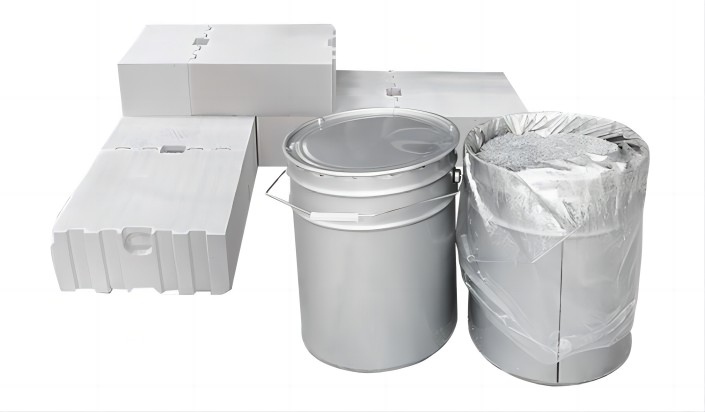
Influence of Aluminum Powder Purity on AAC Block Performance
The purity of aluminum powder significantly impacts the performance of AAC blocks. The high-purity aluminum powder contains minimal impurities, leading to more efficient reactions and a more uniform pore structure.
1. Strength
- Reduced strength with impurities: Impurities in aluminum powder can hinder the reaction, leading to an irregular pore structure. Larger and more irregularly shaped pores weaken the material’s structural integrity.
- Improved strength with high purity: High-purity aluminum powder promotes a more uniform and finer pore structure, enhancing the compressive strength of the AAC block.
2. Porosity
- Optimal porosity: High-purity aluminum powder contributes to a more controlled and predictable porosity, allowing manufacturers to tailor the block’s properties to specific applications.
- Reduced porosity with impurities: Impurities can reduce the overall porosity or create a non-uniform pore distribution, negatively impacting the block’s thermal insulation and acoustic properties.
3. Water Absorption
- Increased absorption with impurities: Impurities can lead to larger and more interconnected pores, increasing the block’s susceptibility to water absorption. This can reduce its durability and resistance to moisture-related damage.
- Reduced absorption with high purity: A uniform and fine pore structure, resulting from high-purity aluminum powder, minimizes water penetration, enhancing the block’s durability.
4. Thermal Conductivity
- Improved insulation: High-purity aluminum powder promotes a pore structure that effectively traps air, reducing thermal conductivity and enhancing the block’s insulation properties.
- Reduced insulation with impurities: Impurities can disrupt the pore structure, increasing thermal conductivity and diminishing the block’s energy efficiency.
Conversely, low-purity aluminum powder can have several detrimental effects on the properties of AAC blocks:
- Reduced gas generation: Impurities can hinder the reaction between aluminum powder and the alkaline components, leading to a lower volume of hydrogen gas and fewer pores.
- Non-uniform pore structure: The presence of impurities can result in an uneven distribution of pores, affecting the block’s overall strength and insulation properties.
- Increased water absorption: A non-uniform pore structure can create larger and more interconnected pores, increasing the block’s susceptibility to water absorption. This can lead to issues such as efflorescence, reduced durability, and potential mold growth.
- Decreased thermal performance: A less efficient reaction and non-uniform pore structure can reduce the thermal insulation properties of the AAC block, making it less energy-efficient.
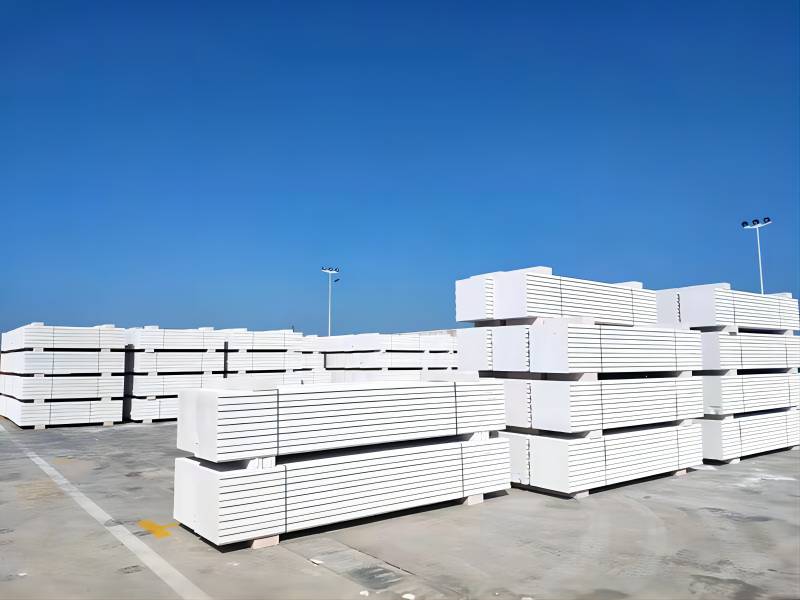
Conclusion
Aluminum powder plays a vital role in the production of AAC blocks, significantly influencing their quality and performance. Its precise usage and high purity are essential for achieving optimal density, strength, and insulation properties. By employing accurate measurement, adjusting raw material ratios, and optimizing production processes, manufacturers can ensure the consistent quality of AAC blocks. The continued focus on research and technological advancements will further enhance the sustainability and efficiency of AAC block production, solidifying its place as a valuable material in modern construction.
References
- Smith, J., & Brown, A. (2020). The Influence of Aluminum Powder on AAC Block Quality. Journal of Construction Materials, 45(2), 123-135.
- Wang, L., & Zhang, H. (2021). High-Purity Aluminum Powder and Its Impact on AAC Block Performance. International Journal of Building Science, 32(3), 456-467.
- Green, D., & Harris, T. (2019). Sustainable Construction with AAC Blocks. Environmental Construction Review, 27(4), 78-89.