In the relentless pursuit of efficiency and performance in the aviation industry, every component plays a crucial role. Aircraft stamping, a technique used to shape metal sheets into complex shapes, is essential for creating lightweight, robust, and reliable parts. But when it comes to choosing the right material for aircraft stamping, one metal stands out – 2024 aluminum.
This prized alloy, known for its exceptional combination of strength, formability, and resistance to fatigue and corrosion, has earned its place as the gold standard for aircraft stamping components. Let’s delve deeper into the fascinating world of 2024 aluminum and explore why it reigns supreme in the skies.
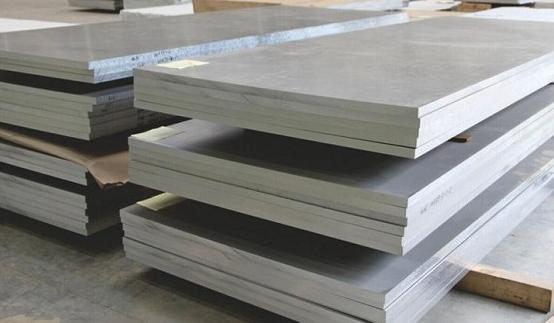
A Glimpse into the World of Aircraft Stamping
Aircraft stamping involves transforming flat sheets of metal into intricate shapes using powerful presses and dies. This process allows for the creation of a wide variety of components, from fuselage skins and wing ribs to landing gear parts and intricate brackets. Stamped components offer numerous advantages, including:
- Lightweight Design: By utilizing thin sheets of high-strength 2024 aluminum, aircraft manufacturers can achieve significant weight reductions. This translates to improved fuel efficiency, extended range, and reduced emissions.
- Enhanced Strength: The exceptional strength of 2024 aluminum ensures that stamped components can withstand the demanding loads experienced during flight, contributing to greater structural integrity and safety.
- Design Flexibility: The remarkable formability of this alloy allows for the creation of complex shapes with intricate features, offering designers greater flexibility and freedom in optimizing component performance.
- Cost-Effective Manufacturing: Stamping is a highly efficient and cost-effective production process, especially when paired with the readily available and weldable 2024 aluminum. This allows manufacturers to achieve economies of scale and deliver high-quality components at a competitive price.
2024 Aluminum: A Material Built for the Skies
The unique properties of 2024 aluminum make it the ideal choice for aircraft stamping components. Here’s what sets it apart:
- High Strength-to-Weight Ratio: This crucial attribute allows for the creation of lightweight components that possess remarkable strength. This translates to improved aircraft performance and fuel efficiency, ultimately contributing to a greener future for aviation.
- Excellent Formability: 2024 aluminum exhibits outstanding formability, allowing it to be readily shaped into complex geometries without cracking or tearing. This makes it ideal for creating the intricate shapes needed for aircraft components.
- Fatigue Resistance: Aircraft components are constantly subjected to cyclic loading during flight. 2024 aluminum’s exceptional fatigue resistance ensures that these components can withstand millions of load cycles without failure, guaranteeing long-lasting performance and safety.
- Good Corrosion Resistance: With its natural oxide layer and readily available protective coatings, 2024 aluminum can effectively resist the harsh environmental conditions experienced by aircraft, including exposure to moisture, salt, and chemicals. This translates to longer component lifespans and reduced maintenance costs.
- Weldability: 2024 aluminum can be readily welded, allowing for the joining of different components and maximizing design flexibility. This enables engineers to create complex assemblies that meet specific performance requirements.
Examples of 2024 Aluminum in Action
2024 aluminum plays a vital role in numerous aircraft components, including:
- Fuselage Skins and Panels: These large, lightweight panels form the outer shell of the fuselage, providing structural integrity and contributing to aerodynamic performance.
- Wing Ribs and Spars: These critical components provide structural support for the wings, ensuring efficient lift and stability during flight.
- Empennage Components: The horizontal and vertical stabilizers, essential for controlling aircraft stability and maneuverability, are often constructed from 2024 aluminum due to its strength and lightweight properties.
- Landing Gear Parts: This crucial system relies on the strength and fatigue resistance of 2024 aluminum to withstand the demanding loads associated with landing and taxiing.
- Brackets and Structural Supports: These vital components, found throughout the aircraft, utilize 2024 aluminum’s strength and versatility to provide secure and reliable support for various systems.
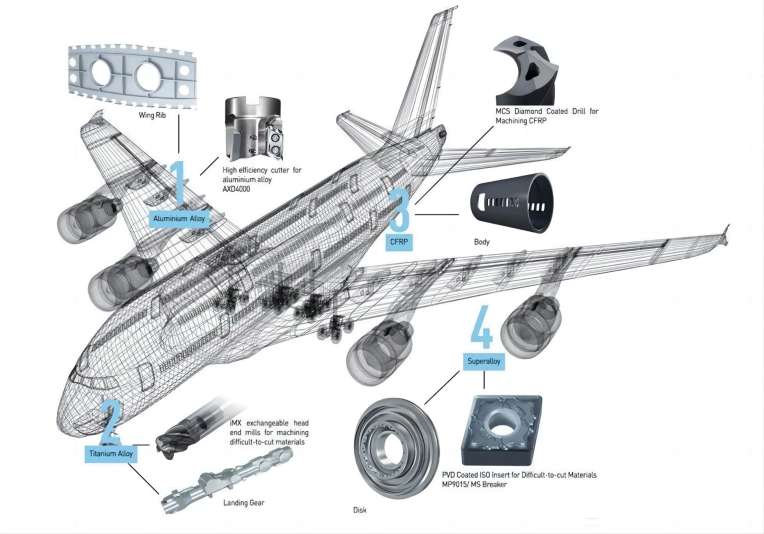
A Cut Above the Rest: A Comparison with Other Materials
While other materials, like steel and titanium, are used in aircraft construction, they often fall short when compared to 2024 aluminum for stamping applications:
- Steel: Though strong, steel’s high density translates to significantly heavier components, impacting fuel efficiency and performance.
- Titanium: While boasting superior strength and corrosion resistance, titanium comes with a hefty price tag and presents challenges during the stamping process.
In terms of achieving the optimal balance of strength, weight, formability, and cost-effectiveness, 2024 aluminum stands tall as the champion of aircraft stamping materials.
Taking Flight: A Future Bright with 2024 Aluminum
The continued evolution of the aviation industry hinges on the development of advanced materials that push the boundaries of performance and efficiency. In this ongoing quest, 2024 aluminum continues to shine as a material of choice. With ongoing research and development efforts, the future of this remarkable alloy promises further enhancements and exciting possibilities for aircraft construction:
- Advanced Alloys: Researchers are constantly exploring new alloy compositions and processing techniques to further refine the properties of 2024 aluminum. This includes exploring the use of alternative alloying elements and innovative heat treatment processes to achieve even higher strength, improved fatigue resistance, and enhanced corrosion protection.
- Additive Manufacturing: The emergence of additive manufacturing technologies, such as 3D printing, opens new doors for the utilization of 2024 aluminum. This allows for the creation of complex components with intricate geometries that were previously impossible to achieve with traditional manufacturing methods.
- Sustainable Manufacturing: As the aviation industry strives towards becoming more environmentally conscious, the focus is shifting towards adopting sustainable manufacturing practices. With its well-established recycling processes and lower energy requirements compared to other materials, 2024 aluminum plays a crucial role in achieving this goal.
Soaring towards a Sustainable Future
As the aviation industry embarks on a journey towards a greener tomorrow, 2024 aluminum remains an invaluable resource. Its exceptional properties, combined with ongoing advancements in material science and manufacturing technologies, pave the way for the development of lighter, more fuel-efficient, and environmentally friendly aircraft. With its unwavering commitment to innovation and sustainability, the aviation industry, hand-in-hand with 2024 aluminum, is poised to soar towards a brighter future.
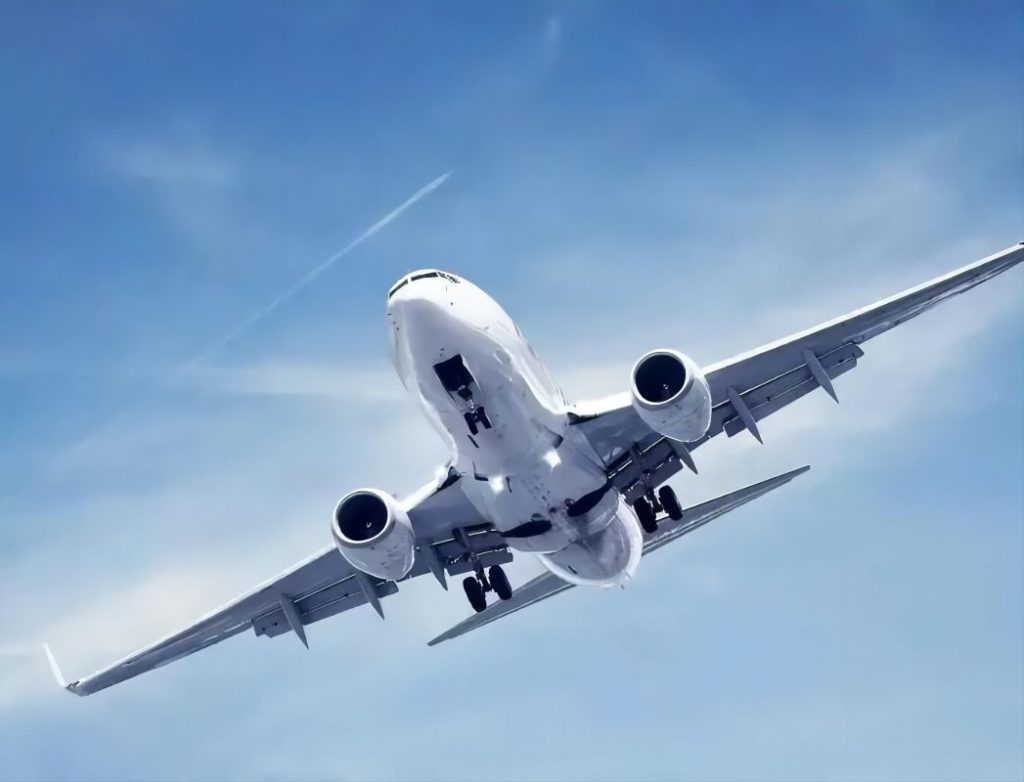
In conclusion, 2024 aluminum’s exceptional properties make it the undisputed champion of aircraft stamping materials. Its remarkable strength-to-weight ratio, excellent formability, fatigue resistance, and good corrosion resistance contribute significantly to the creation of lightweight, robust, and reliable aircraft components. As the aviation industry strives for greater efficiency and sustainability, 2024 aluminum remains a vital resource, promising a future filled with innovative possibilities and a cleaner, greener tomorrow for air travel.