In today’s fast-paced technological world, electronics are becoming more compact, more powerful, and more complex. With these advancements, however, comes a growing concern: heat management. Whether it’s a smartphone, a laptop, or a high-performance server, electronic devices generate heat that, if not properly managed, can lead to reduced performance, shortened lifespans, and even catastrophic failure. Effective heat dissipation is essential to ensure that electronics continue to operate at their best. Among the many materials used in the thermal management of electronics, aluminum stands out as the metal of choice. Thanks to its unique combination of properties, aluminum has become an indispensable material in the design of heat management systems. This article will explore why aluminum excels at heat dissipation, its practical applications, and its benefits in electronic cooling.
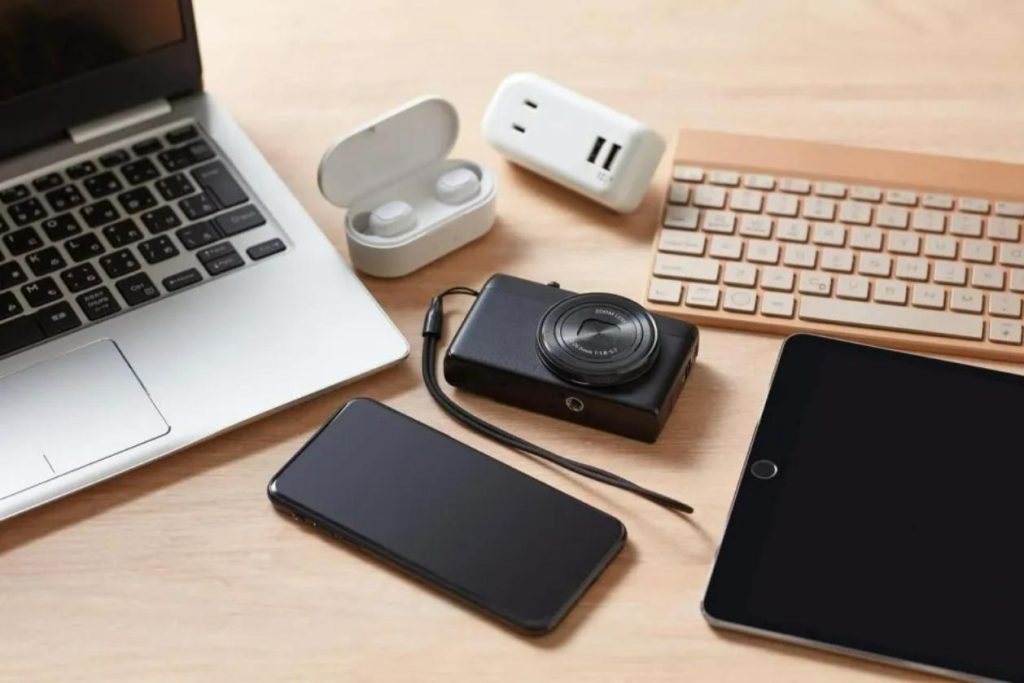
The Challenges of Heat in Electronics
Heat generation is an inevitable byproduct of electrical components in motion. Whether it’s in a microprocessor, graphics card, or a power supply unit, the energy consumed by these devices is often released as heat. The challenge lies in managing that heat effectively to maintain optimal performance and protect the integrity of the device.
Why Heat Management Matters
Electronics, especially those with high performance or small form factors, are particularly vulnerable to the effects of heat. When devices overheat, they can experience:
- Decreased Performance: Components such as CPUs and GPUs will throttle their performance to avoid further heating, leading to a slowdown.
- Reduced Lifespan: Heat accelerates wear and tear on components, causing them to fail prematurely.
- Safety Risks: Excessive heat can result in fires, battery leaks, or other hazardous outcomes.
- System Instability: Heat buildup can cause malfunctions, crashes, or system shutdowns, impacting reliability.
To prevent these issues, effective heat dissipation mechanisms are vital. Engineers and manufacturers have to design systems that can maintain safe operating temperatures while not adding undue weight or cost to the device.
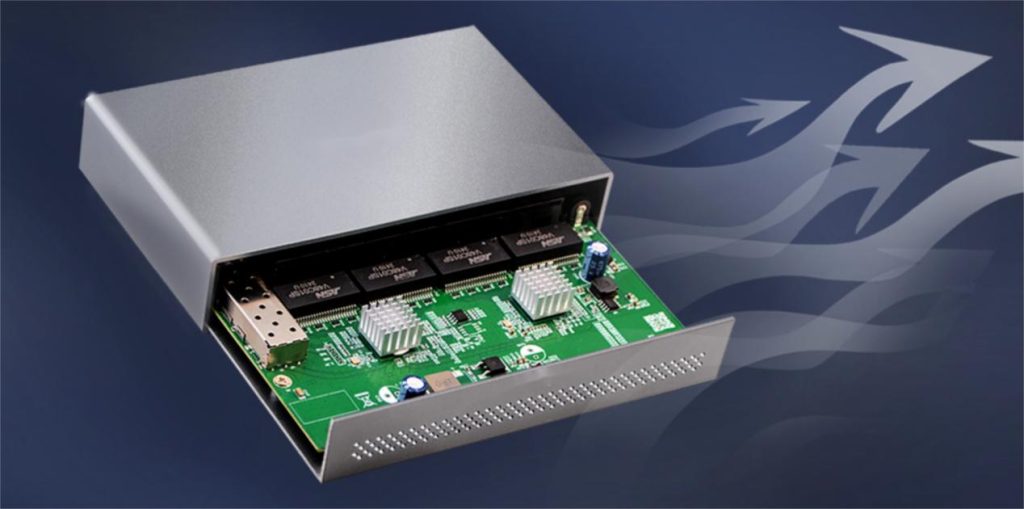
Why Aluminum Excels
Among various metals used for heat management, aluminum has emerged as a top contender due to its ideal combination of properties that address both the performance needs and cost constraints in modern electronics. But why is aluminum so special when it comes to thermal management?
Thermal Conductivity
Aluminum’s thermal conductivity is one of its most significant attributes. While it’s not as high as copper or silver, aluminum’s thermal conductivity is more than sufficient for most electronic applications. It allows heat to travel quickly through the material and dissipate efficiently. This makes it ideal for heat sinks, cooling fins, and other thermal management devices.
Lightweight
Aluminum is incredibly lightweight compared to other metals like copper or steel. This is especially important in portable electronics such as smartphones, laptops, and tablets, where weight is a critical design factor. Its lightness doesn’t compromise its ability to dissipate heat, which makes it a great choice for energy-efficient and lightweight devices.
Cost-Effective
While copper has better thermal conductivity, aluminum is significantly cheaper. This makes it a highly cost-effective material, particularly for large-scale manufacturing. For industries where large volumes of electronic devices are produced, such as consumer electronics or automotive applications, the lower cost of aluminum helps keep production costs down without sacrificing performance.
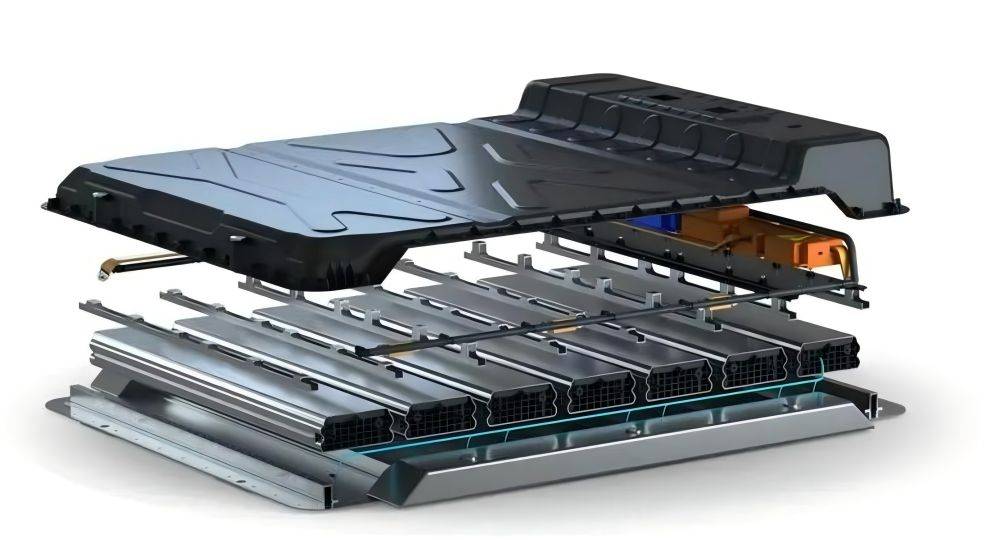
Corrosion Resistance
Aluminum has excellent resistance to corrosion, even in harsh environments. This resistance extends the longevity of heat management components, ensuring that aluminum parts remain effective over the long term, without needing frequent replacements.
Flexibility and Ease of Fabrication
Aluminum is also incredibly versatile. It can be extruded, machined, and shaped into various forms, such as thin fins for heat sinks or compact enclosures for electronic devices. Its malleability allows designers to create components tailored precisely to the needs of the device they are cooling.
In summary, aluminum excels at thermal management due to its effective thermal conductivity, lightweight nature, cost-effectiveness, corrosion resistance, and fabrication flexibility. These properties make it the ideal metal for electronic heat management, especially as devices continue to shrink in size while increasing in power.
Applications of Aluminum in Electronic Cooling
Given its advantages, aluminum is used in a wide array of electronic devices to manage heat. The applications of aluminum in thermal management range from consumer electronics to industrial equipment, and its role in active cooling solutions is just as important as in passive cooling mechanisms.
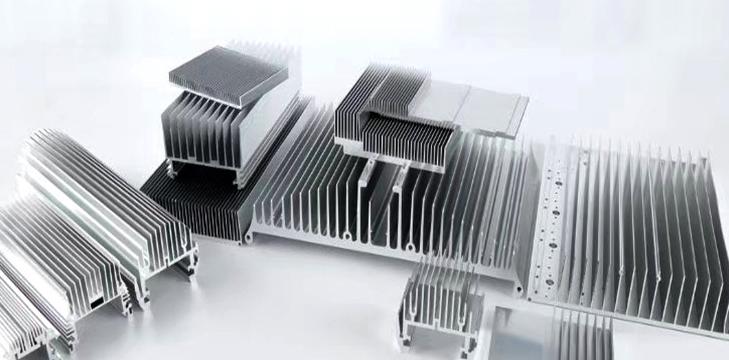
Heat Sinks
One of the most common uses of aluminum in electronics is in heat sinks. These are metal components attached to heat-sensitive parts, such as processors or LEDs, designed to absorb and dissipate excess heat. Aluminum heat sinks are lightweight, easy to manufacture, and effective at transferring heat away from critical components.
Cooling Fins and Thermal Plates
Aluminum is also used in cooling fins, which are integral parts of heat sinks, and thermal plates, which are designed to spread heat across a surface more evenly. These fins and plates are designed to maximize surface area, which enhances heat dissipation by increasing airflow or contact with a cooling medium.
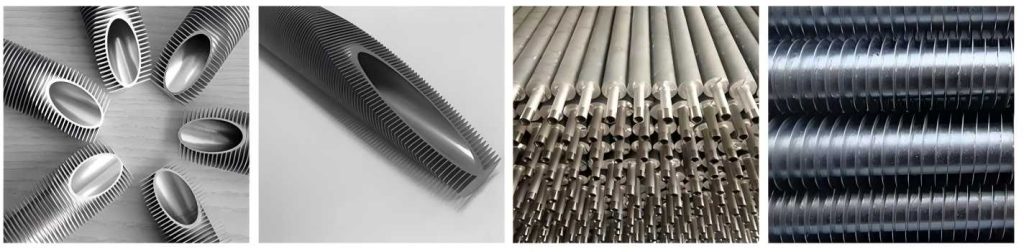
Enclosures and Casings
In many electronic devices, the enclosures or casings are made from aluminum. Not only do these housings protect internal components, but they also contribute to thermal management. The aluminum case can act as a heat sink, helping to cool the device from the outside.
Power Electronics
In high-power applications, such as electric vehicles and renewable energy systems, aluminum is used in power electronic modules. These modules often require efficient heat management because they deal with high currents that generate significant heat. Aluminum’s thermal conductivity and durability make it a prime material for power electronics.
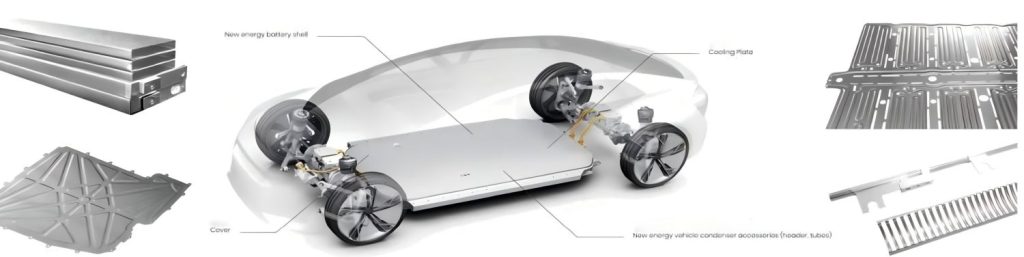
Computing and Data Centers
Aluminum is commonly used in data centers for server cooling. With the massive amounts of heat generated by servers, aluminum is employed in various forms, such as heat exchangers, thermal plates, and heat sinks, to ensure that the servers run at optimal temperatures.
From consumer devices to industrial systems, aluminum plays an essential role in electronic cooling. In electronics, the type of aluminum chosen depends on the specific requirements of the application. For most general electronics, 3000 series, 5000 series, and 6000 series alloys are the most commonly used due to their balance of strength, corrosion resistance, and workability. 1000 series alloys are popular in applications where high conductivity and corrosion resistance are needed, while 2000 series alloys are used for higher-strength components, albeit with some trade-offs in corrosion resistance.
As the demand for electronics grows and evolves, especially in fields like automotive electronics, power electronics, and high-performance computing, aluminum’s versatility and range of alloys will continue to play a critical role in thermal management and structural applications.