When the aluminum profile is extruded and pressurized, the air will remain in the aluminum profile, causing bubbles to appear inside and on the surface of the aluminum profile, causing defects that cannot be resolved entirely, and making the aluminum profile a waste product. To prevent air from entering the aluminum profile, it is necessary to figure out why it is brought in.
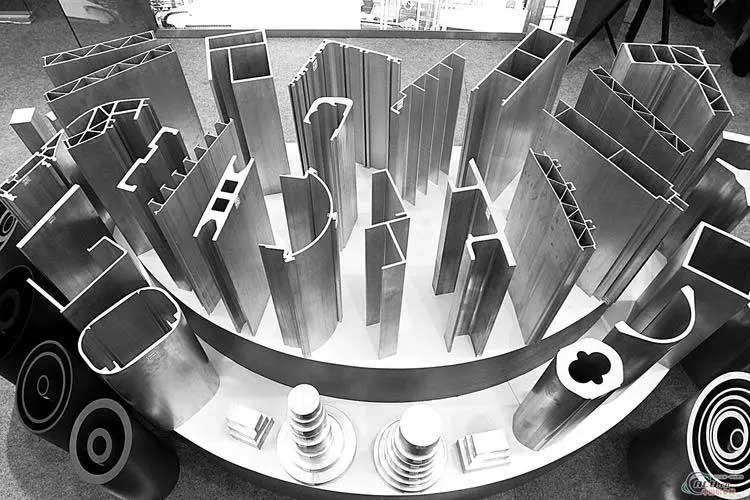
The following are the main causes of trapped air inside four extruded aluminum profiles:
Hot shearing of long rods leads to residual air
The shear plane formed when the column rod is thermally sheared will never be perfect and vertical.
The simple thermal shearing of long rods of industrial aluminum profiles will make the bending of the column rods very serious, resulting in an oval cross-section of the aluminum profile and a very large rounded corner at the sheared end. Even with the latest long rod shears, the edge angles of the sheared rods will always be rounded, and these rounds are the best places for air to remain.
Solution: Carry out a standard inspection on aluminum rods, and resolutely put an end to unqualified aluminum rods.
Upsetting causes air to remain
Upsetting causes air to remain. Only when the diameter of the aluminum ingot cylinder is larger than that of the column rod, the column rod can be put into the cylinder containing the aluminum ingot.
After applying pressure to the column rod inside the aluminum ingot cylinder to cause the column rod to expand to the diameter of the ingot cylinder, the gas carried must be discharged. The gas is not exhausted, and it remains in the aluminum ingot and eventually turns into air bubbles.
Solution: Configure the extrusion gasket according to the minimum size of the extrusion cylinder lining, replace the extrusion cylinder regularly, check the extrusion cylinder and extrusion pad corrosion, measure the extrusion cylinder, extrusion pad inner and outer diameters Size to configure the appropriate extrusion gasket; clean the extrusion cylinder with a cleaning gasket once every shift, and regularly corrode the extrusion cylinder.
The connection of two aluminum rods leads to the residual air
Air is trapped due to the contact of the two aluminum rods. Because the surfaces of the two stubs are flat, the probability of air being carried in is very small.
The quality of the saw cut directly interferes with the amount of air carried between the two stubs. At present, there is a high-tech that can prevent two short column rods from connecting and eliminate the possibility of air entry.
Solution: Determine the aluminum rod with a reasonable rod length according to the process parameters such as profile weight and output count.
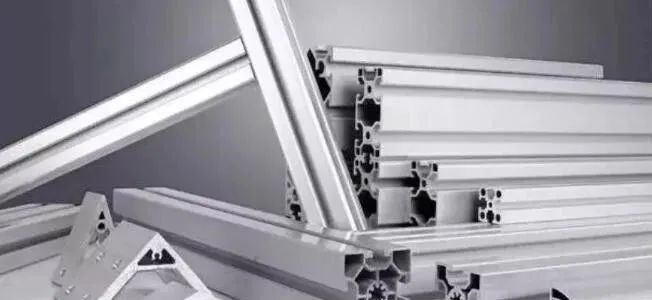
Extruded aluminum profiles lead to air entrapment
When extruding aluminum profiles, it is necessary to avoid the entry of air, to avoid the situation of residual air, which will cause various defects in the post-processing.
1. Improper oiling causes air bubbles in the product.
Solution: use the correct method of oiling and reduce the amount of oiling; strengthen the training of employees’ pre-job operation techniques;
2. The excess pressure is too thin, causing the metal of the split hole to be pulled out during shearing, leaving a gap in the split hole of the mold.
Solution: According to the tonnage of the extruder, leave a reasonable excess thickness, and determine the aluminum rod with a reasonable rod length according to the process parameters such as the single weight of the profile and the number of discharge counts;
3. The extrusion die is designed with a flat die welding chamber, and the diversion hole of the diversion die is too large to cause air bubbles to flow into the cavity.
Solution: Reduce the size of the welding chamber of the flat die, reduce the die hole of the splitter die, and keep the distance from one side of the extrusion cylinder to more than 5MM.
Design molded cause bubbles of aluminum profiles
For example, in the mold design of the motor casing, in the production process of the aluminum profile of the motor casing, there are often phenomena such as air bubbles in the product due to the mold. At the same time, the life of the mold is not long, and the phenomenon of premature failure of the mold occurs. After the mold fails, the interchangeability of the motor housing is poor.
This article introduces the design and production drawings of a typical motor shell aluminum profile mold, which effectively solves the problems that often occur in the profile production process, and can be used as a reference for peers.
Conclusion
When the aluminum profile extruder is pressurized, air remains, causing bubbles to appear inside and on the surface of the aluminum profile, resulting in defects that cannot be resolved entirely, making the aluminum profile a waste. Through the analysis and comparison of traditional and improved aluminum rod casting, extrusion and mold design and manufacturing process, it can be known that to improve the output efficiency of extruded profiles, to improve the control of extrusion surface requirements, to extrude aluminum profiles The solution to the bubbles in production is critical.