The die-casting shell is formed by a mold, so the processing time is short and the cost is relatively low. However, aluminum die casting is difficult to anodize. It is believed that many manufacturers should have found out when surface treatment of various series of aluminum materials that aluminum die casting is not suitable for anodizing treatment. This is all determined by the composition of aluminum die casting and the characteristics of anodizing, so why is aluminum die casting unsuitable for anodizing?
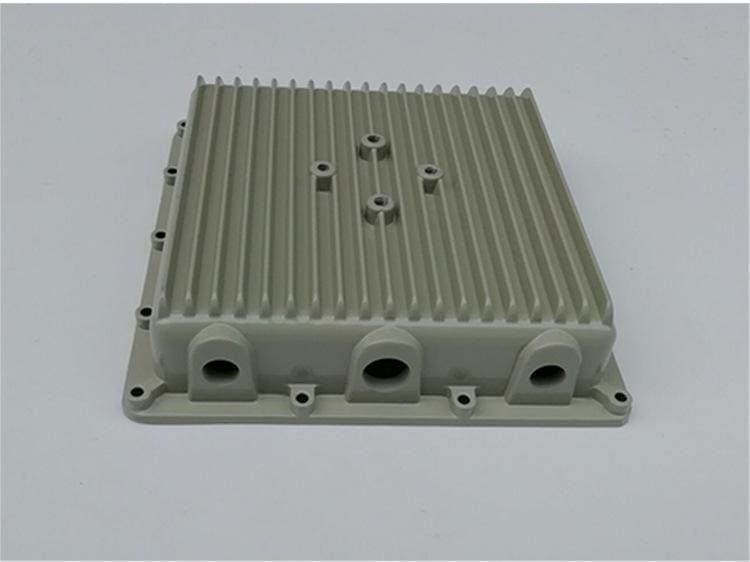
Why is Die Cast Aluminum Difficult to Anodize?
Anodizing
Anodizing treatment is an electrochemical method. In a suitable electrolyte, the alloy parts are used as the anode, and stainless steel, chromium, or the conductive electrolyte itself is used as the cathode. Under certain voltage and current conditions, the anode is oxidized, thereby The process of obtaining an anodized film on the surface of the workpiece requires anodizing with sulfuric acid in the process of anodizing and coloring.
Limitations of Sulfuric Acid Anodizing on Aluminum Alloys
1. The presence of alloying elements will reduce the quality of the oxide film. Under the same conditions, the oxide film obtained on pure aluminum is the thickest, the hardness is the highest, the corrosion resistance is the best, and the uniformity is the best. For aluminum alloy materials, to obtain a good oxidation effect, it is necessary to ensure that the content of aluminum is not less than 95% under normal circumstances.
2. In the alloy, copper will make the oxide film reddish, destroy the quality of the electrolyte, and increase oxidation defects; silicon will make the oxide film gray, especially when the content exceeds 4.5%, the effect is more obvious; It will then appear as black spots.
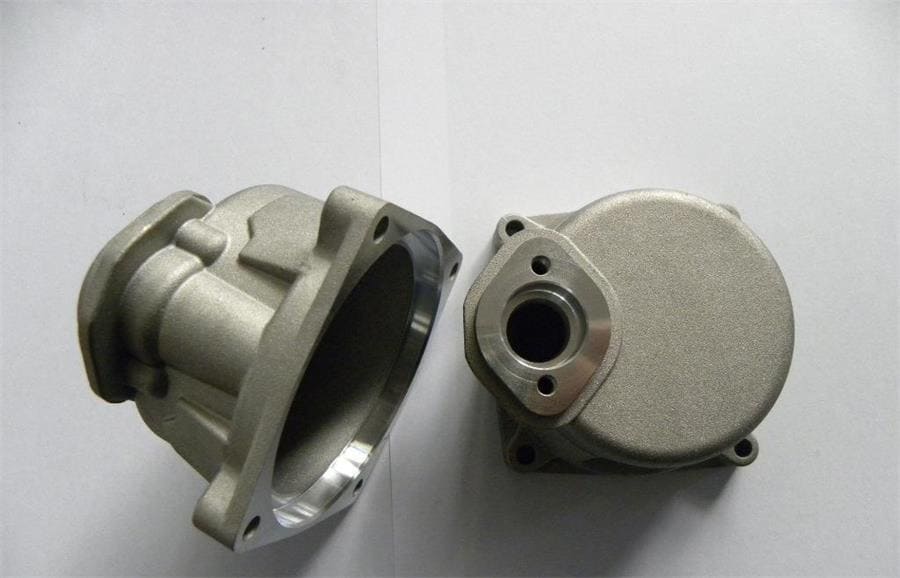
3. Anodizing requires that the aluminum surface is free of impurities, and the aluminum material is relatively pure because the anodized film must be uniform and flat. The excessive presence of impurities and other components will inevitably affect the thickness of the film formed during anodization, and even directly affect whether the film is formed. The most important thing is that other metal elements may directly change the color of the film when the anodized film is formed, which has a direct impact on the dyeing after anodization.
4. Cast aluminum alloys and die castings generally contain high silicon content. Commonly used die casting aluminum alloys can be mainly divided into three categories:
One is aluminum-silicon alloy, mainly including YL102 (ADC1, A413.0, etc.), YL104 (ADC3, A360).
The second is aluminum-silicon-copper alloy, mainly including YL112 (A380, ADC10), YL113 (A383, ADC12), and YL117 (B390, ADC14).
The third is aluminum-magnesium alloy, mainly including 302 (5180, ADC5, ADC6).
For aluminum-silicon alloys and aluminum-silicon-copper alloys, as the name implies, in addition to aluminum, silicon and copper are the main components. Usually, the silicon content is between 6-12%, which mainly improves the fluidity of the alloy liquid. The copper content is second, mainly to enhance the strength and tensile force. The iron content is usually between 0.7-1.2%, and within this ratio, the demolding effect of the workpiece is the best.
It can be seen from its composition that such alloys cannot be oxidized and colored. Even if ht412 special ash remover for die-casting aluminum is used, the anodic oxide film may be dark, and it is difficult to obtain a colorless and transparent oxide film. As the silicon content increases, the color of the anodized film varies from light gray to dark gray to dark gray. Therefore, cast aluminum alloys are not suitable for traditional anodizing.
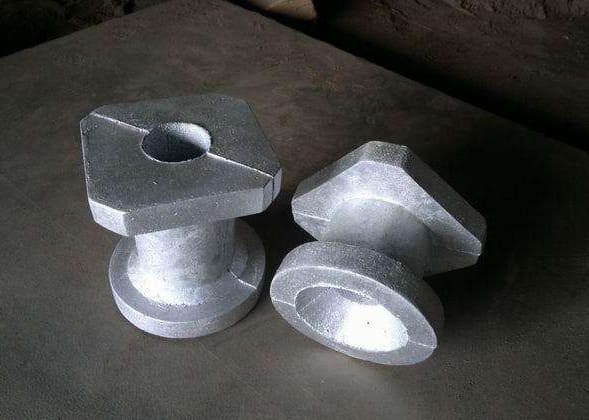
How to Solve the Difficulty of Anodizing Cast Aluminum?
But die cast aluminum also has anodizing solutions. Die-casting parts can complete the structure and angular lines that are difficult to achieve for forging parts, car parts/CNC parts. The quality of the die casting is very important to the oxidation quality. A small change and detailed process control determine the quality of the anode.
Manufacturers engaged in the oxidation of die-casting parts must scientifically control the runner technology of the mold, the die-casting process, and the post-processing method. With this series of strict control processes, the smooth production of the oxidation quality can be ensured. This includes mold runner, gate design, mold temperature control; the use of raw materials, and generally use of ht412 special ash remover for die-casting aluminum to remove surface black ash and avoid pollution factors.
Conclusion
CHAL is one of the professional aluminum products suppliers. We can provide you with alumninum tubes, aluminum profiles, aluminum coils, etc. These profiles are widely used in various industries. The company integrates production, sales, and service, and is committed to the improvement and innovation of aluminum products with the concept of quality-oriented, technology-leading, and service-winning.