For decades, condenser headers, the workhorses of heat exchangers, relied on traditional materials like steel or copper. While these served their purpose, limitations in weight, cost, and efficiency often hampered their performance. However, a revolution is brewing in the world of condenser design, and the champion leading the charge is welded aluminum pipe.
This lightweight champion boasts a unique set of properties that are transforming the landscape of condenser headers. From shedding significant weight to boosting heat transfer efficiency, aluminum is not just an alternative, it’s a game-changer. But why exactly is this metal making such a splash? In this article, we’ll delve into the compelling reasons why welded aluminum pipe is rapidly becoming the go-to choice for condenser headers across various industries.
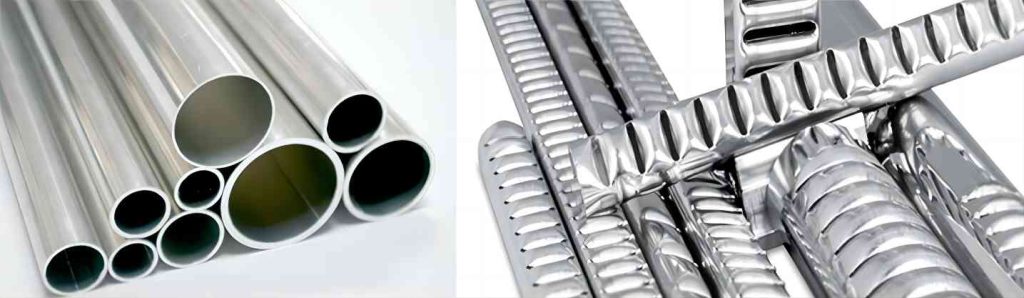
Advantages of Welded Aluminum Pipes in Condenser Headers
Welded aluminum pipes offer several significant advantages over traditional materials like steel or copper in condenser headers. These advantages make them a popular choice across various industries, including HVAC, automotive, power generation, and more. Here are some key benefits:
1. Lightweight
Aluminum possesses the highest strength-to-weight ratio among commonly used condenser header materials. This translates to:
- Reduced weight: Condenser units become lighter, leading to easier installation, handling, and portability.
- Improved energy efficiency: Less weight means less energy is required to operate the system, lowering operational costs and environmental impact.
- Enhanced performance: In vehicles, lighter condensers contribute to better fuel efficiency and overall performance.
2. Cost-effectiveness:
Aluminum itself is typically less expensive than steel or copper. The efficient manufacturing process of welded pipes further reduces production costs. Lightweight design often lowers transportation and installation costs.
3. Superior Heat Transfer:
Aluminum has excellent thermal conductivity, meaning it transfers heat much more efficiently than traditional materials. This leads to improved cooling performance and smaller header sizes for equivalent cooling capacity.
4. Corrosion Resistance:
Aluminum naturally offers good corrosion resistance, especially in environments with neutral or slightly acidic conditions. Additional protection through cladding or anodizing can further enhance resistance for specific applications.
5. Formability and Versatility:
Aluminum is highly malleable and can be easily shaped into complex designs, accommodating diverse header configurations. This flexibility allows for optimized layouts and integration with other components.
6. Weldability:
Modern welding techniques like high-frequency induction welding or laser welding are well-suited for aluminum, creating strong and reliable joints. This enables the fabrication of complex headers with leak-proof connections.
7. Additional Advantages:
- Environmentally friendly: Aluminum production has a lower environmental impact compared to steel or copper.
- Hygienic properties: Aluminum’s smooth surface makes it suitable for applications in the food and beverage industry.
- Aesthetics: Aluminum offers a clean and modern appearance compared to other materials.
It’s important to note that while aluminum offers numerous advantages, there are also limitations to consider, such as lower ultimate strength compared to steel. However, advancements in alloys and design practices are continuously addressing these limitations, making welded aluminum pipes an increasingly compelling choice for condenser headers.
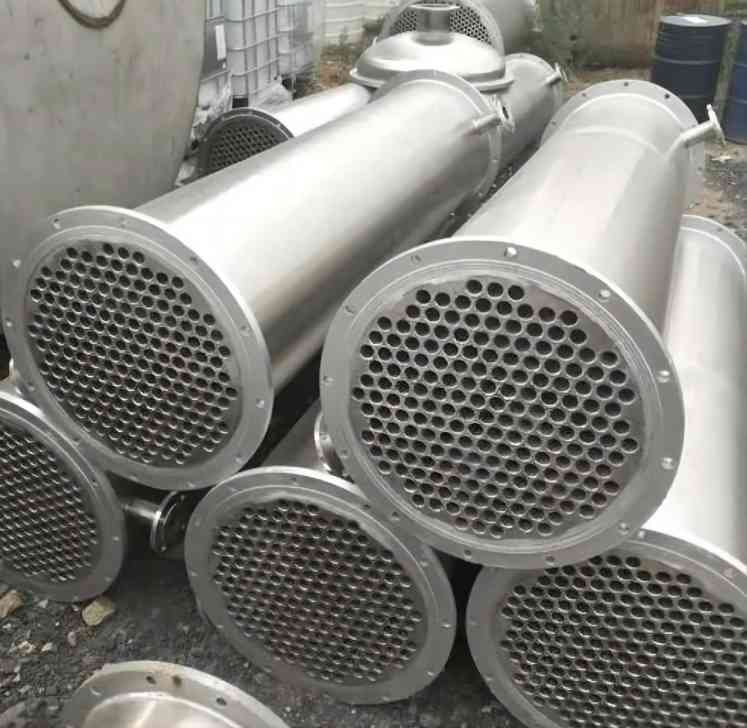
Applications of Welded Aluminum Pipes in Condenser Headers
The impressive features of welded aluminum pipes have led to their adoption across various industries, revolutionizing condenser header design. Here are some key applications:
- HVAC & Refrigeration: Air conditioners, chillers, and heat pumps: Aluminum’s lightweight construction significantly reduces weight, impacting installation ease and portability. Additionally, its superior heat transfer enhances cooling efficiency while lowering energy consumption.
- Automotive Industry: Radiators and condensers in cars, motorcycles, and electric vehicles: The weight reduction translates to improved fuel efficiency and overall vehicle performance. Aluminum’s formability allows for compact and optimized designs, enhancing aesthetics and integration with other components.
- Power Generation: Steam condensers in power plants: The excellent heat transfer properties optimize cooling efficiency, contributing to better plant performance. Aluminum’s corrosion resistance is crucial in handling high-temperature steam environments.
- Marine and Offshore Applications: Heat exchangers in ships and oil rigs: Lightweight construction is essential for minimizing weight on marine vessels. Aluminum’s corrosion resistance is vital in harsh saltwater environments.
- Food and Beverage Industry: Processing equipment and refrigeration systems: Smooth surfaces and hygienic properties make aluminum ideal for applications where cleanliness is paramount. Ease of cleaning further enhances its suitability.
- Aerospace and Defense: Potential applications in aircraft and spacecraft: The weight reduction is crucial for maximizing flight performance and fuel efficiency. Thermal management needs, especially in spacecraft, can be addressed through aluminum’s efficient heat transfer.
The future of welded aluminum pipes in condenser headers remains bright, as ongoing research and advancements further expand their potential. Their combination of performance, cost-effectiveness, and sustainability makes them a compelling choice for various industries seeking efficient and eco-friendly solutions.
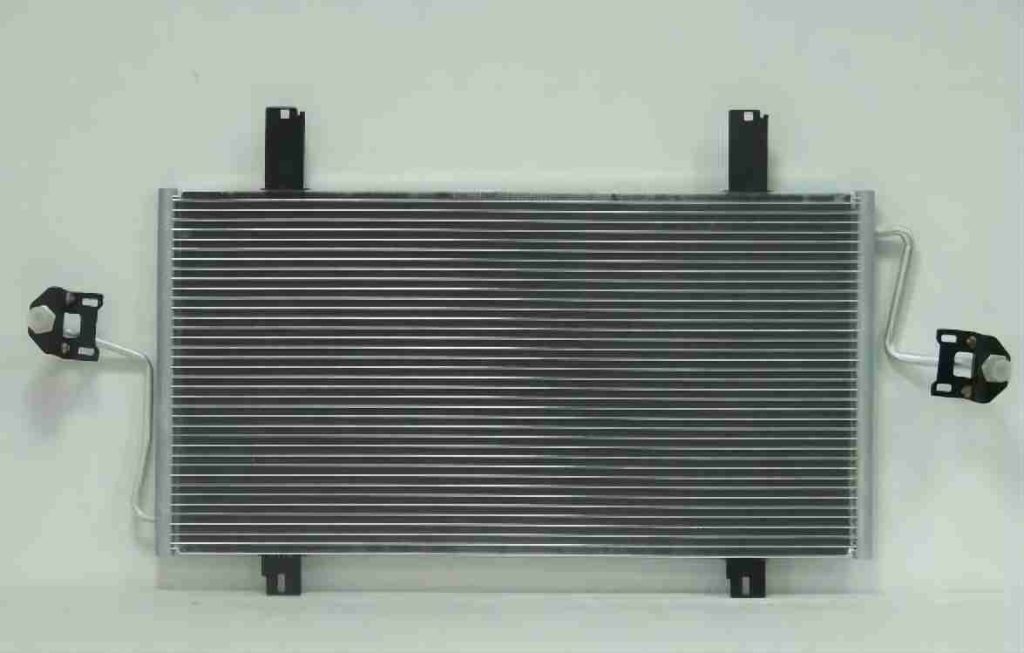
Conclusion
The reasons for embracing welded aluminum pipe in condenser headers are numerous and compelling. Its lightweight nature translates to reduced energy consumption and improved mobility, while its superior heat transfer ensures optimal cooling performance. Additionally, its natural corrosion resistance and versatile formability make it a reliable and adaptable choice for diverse applications.
With ongoing advancements in alloys, welding techniques, and design optimization, the future of aluminum in condenser headers is even brighter. Its environmental benefits and potential for wider adoption across industries make it a sustainable and efficient solution for the years to come.